Samochód sportowy Lotus Type 62-2, przywrócony do życia przez konstruktora Anta Ansteada i byłego mistrza Formuły 1, kierowcę wyścigowego Jensona Buttona, był możliwy tylko dzięki produkcji addytywnej. Jak pokazuje nowy serial na Discovery+, żadna inna technologia nie mogła zapewnić takiej swobody projektowania, elastyczności i kosztów, jak druk 3D w technologii FDM i żywicy.

“Radford Returns” opowiada o odradzaniu się sztuki budowania nadwozi przy użyciu technologii na miarę XXI wieku. W programie występują Anstead i Button, którzy dokumentują budowę retro-nowoczesnego supersamochodu Lotus Type 62-2 oraz szerokie zastosowanie przez nich druku 3D.
Widzowie mają okazję przyjrzeć się od środka procesowi od projektowania do tworzenia prototypów, oprzyrządowania i wreszcie produkcji części przy użyciu technologii druku 3D Stratasys FDM, PolyJet i stereolitografii. W rzeczywistości, w projekcie wykorzystano ponad 500 części drukowanych w 3D.
“Technologia druku 3D firmy Stratasys dała nam swobodę projektowania i możliwość łatwego tworzenia niestandardowych, jednorazowych elementów i części dla tych dwóch prototypowych pojazdów”, powiedział gospodarz Ant Anstead. “Dało nam to możliwość pełnego wykorzystania niestandardowej budowy nadwozi, ale z wykorzystaniem nowoczesnych procesów i technologii XXI wieku.
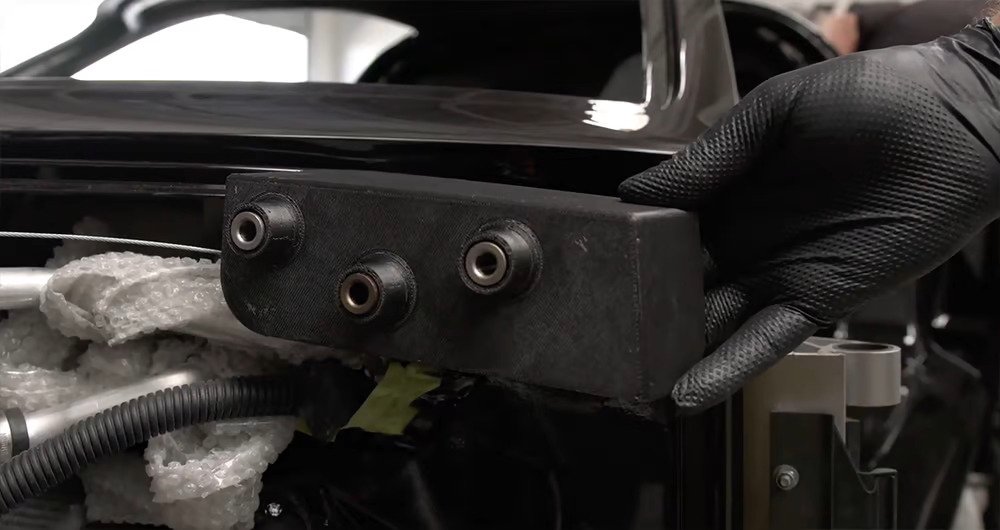
Aby wyprodukować dwa pierwsze samochody, części zostały wydrukowane 3D w Radford Studio, w firmie Aria Group zajmującej się projektowaniem i inżynierią motoryzacyjną oraz w Stratasys Direct Manufacturing. Korzystając z systemu GrabCAD Shop firmy Stratasys, zespół Radford zaplanował i śledził swoje wydruki 3D w pięciu lokalizacjach na całym świecie, używając jednocześnie floty do 20 drukarek 3D Stratasys. W skład zestawu drukarek Stratasys wchodziły drukarki 3D F900, F770, Fortus 450mc, F370 i J55, z których każda była wykorzystywana do osiągnięcia różnych pożądanych rezultatów dla każdej części.
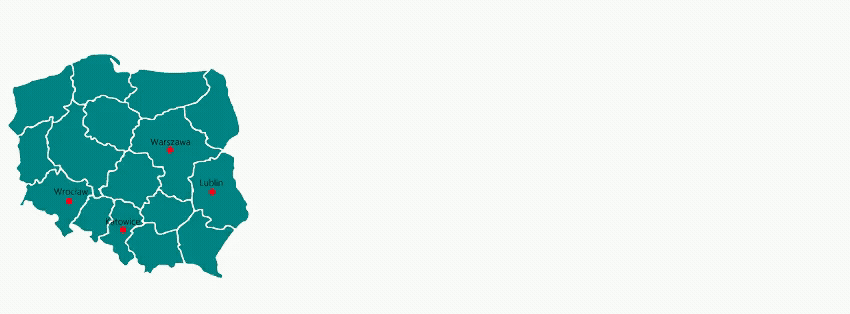
Dzięki różnym drukarkom 3D i technologiom zespół był w stanie wyprodukować takie części, jak duży kompozytowy rdzeń sandwicza ściany ogniowej, wydrukowany w dwóch połówkach na drukarce Stratasys F900 z żywicy Ultem 1010. Część została połączona w jeden element, a następnie owinięta włóknem węglowym bez użycia narzędzi do układania. Konstrukcja ściany ogniowej obejmowała skomplikowane elementy montażowe głośników wewnętrznych, mocowania wlewu paliwa i przestrzeni bagażowej.

Elementy zewnętrzne, od obudów lusterek bocznych i kanałów chłodnicy po otwory wentylacyjne nadwozia, zostały wydrukowane w technologii FDM z włókna węglowego Nylon 12 i materiałów ASA. Wsporniki montażowe w całym samochodzie również zostały wydrukowane 3D z włókna węglowego Nylon 12, nie tylko ze względu na wymogi wytrzymałościowe i swobodę projektowania, ale również w celu dotrzymania harmonogramu projektu.
Integracja technologii druku 3D w warsztacie Radforda nie jest niczym nowym w branży motoryzacyjnej. “To ekstremalny przykład czegoś, co widzimy na co dzień w przemyśle samochodowym,” mówi Pat Carey, starszy wiceprezes ds. rozwoju strategicznego w Stratasys. “Każdy, kto inwestuje w nowe pojazdy, chce mieć możliwość głębszego dostosowania ich do swoich potrzeb, a druk 3D pomaga to umożliwić”.

Żródło: https://all3dp.com