„Większość tytanowych części AM jest budowana przy użyciu technologii proszkowego łoża” — zgodnie z raportem firmy konsultingowej Ampower . „Podczas gdy łączenie proszkowe jest wykorzystywane do produkcji lekkich komponentów dla lotnictwa i wyścigów, a także implantów medycznych, łączenie strumieniowe jest zwykle wykorzystywane do produkcji mniejszych instrumentów medycznych z tytanu”.
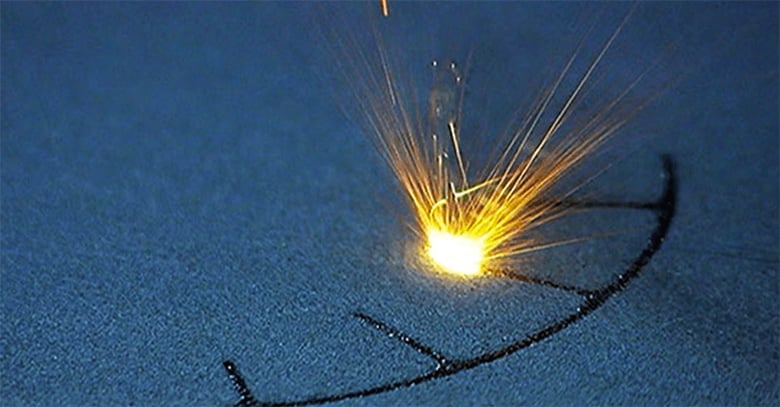
Laser powder bed fusion (LPBF) to technologia produkcji wykorzystująca sproszkowany metal łączony dzięki lasera o dużej mocy. LPBF wytwarza część poprzez dodanie warstwy materiału do poprzedniej. Na podstawie adekwatności stopu na bazie tytanu, który ma zostać przetworzony, parametry przetwarzania LPBF muszą zostać zoptymalizowane i dostrojone w celu kontrolowania porowatości, mikrostruktury i końcowych adekwatności materiału.
Fuzja proszkowa wiązką elektronów (EB PBF) , zwana również topieniem wiązką elektronów (EBM), jest podobnym procesem, ale wykorzystuje wiązkę elektronów o większej mocy zamiast lasera. Wysoka temperatura procesu wiązki elektronów powoduje wolniejsze chłodzenie pojedynczych warstw, a zatem grubszą mikrostrukturę w porównaniu z LPBF, zgodnie z Ampower. Ta cecha jest zaletą dla wielu implantów medycznych.
W obu procesach łączenia proszkowego, drukarki 3D do metalu zaczynają pracę od metalowego łoża proszkowego, które jest selektywnie skanowane. Wszystkie informacje geometryczne są przekazywane do systemu drukowania z modelu CAD zdefiniowanego wcześniej w oprogramowaniu do modelowania 3D. Materiał proszkowy charakteryzuje się głównie cechami, takimi jak morfologia cząstek (nieregularna lub sferyczna) i rozkład wielkości cząstek. Morfologia sferyczna jest pożądana, aby umożliwić dobrą płynność proszku po zakończeniu procesu drukowania. Proces, w którym powstaje proszek, określa jego ostateczne cechy. Proszki metalowe można wytwarzać przez rozpylanie gazowe, rozpylanie rotacyjne, proces elektrody obrotowej plazmowej i rozpylanie wodne. Podsumowując, wysokiej jakości proszek wytworzy wysokiej jakości części.
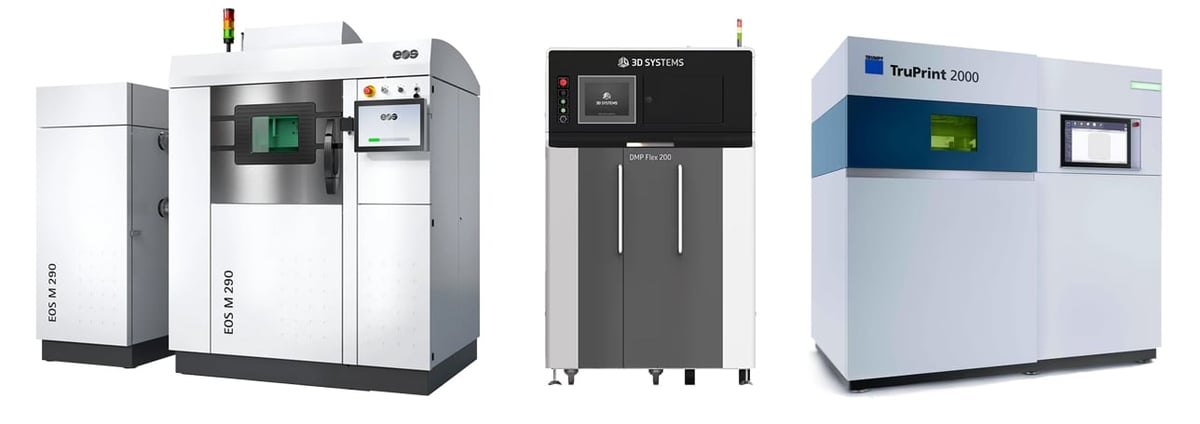
Drukarki 3D drukujące z tytanu
Nie każda drukarka 3D do metalu może drukować z tytanu, jednak obecny rynek systemów druku 3D oferuje szeroką gamę drukarek 3D do metalu, umożliwiających obróbkę różnych stopów na bazie tytanu.
Drukarki laserowe do łączenia proszkowego (LPBF) z możliwościami tytanowymi
- Firma 3D Systems oferuje trzy rodzaje materiału tytanowego, które są kompatybilne z wieloma drukarkami 3D PBF.
- Firma EOS oferuje pięć opcji materiałów tytanowych, które można stosować w czterech drukarkach 3D wykorzystujących technologię stapiania proszków metalowych.
- Colibrium Additive oferuje tytan i stopy tytanu do drukarek 3D serii M2 5.
- Nikon SLM Solutions dostarcza trzy stopy tytanu do swoich drukarek 3D.
- Velo3D ma rozwiązanie tytanowe dla swojej rodziny drukarek 3D Sapphire.
- Laserowa drukarka 3D do fuzji metali firmy Trumpf jest przeznaczona do produkcji części tytanowych.
- Drukarki 3D do metalu firmy Renishaw cieszą się popularnością przy produkcji części tytanowych w medycynie i stomatologii.
- Firma Markforged oferuje jeden stop tytanu w swojej drukarce 3D PX100 wykorzystującej technologię spoiwa.
- Firma Desktop Metal oferuje opatentowany filament wypełniony stopem tytanu do swojej technologii wytłaczania Bound Metal Deposition.
- Meld Manufacturing to wyjątkowa technologia półprzewodnikowa przeznaczona do produkcji większych części.
- Tytan 6Al-4V, gatunek 5 jest najczęściej stosowanym stopem tytanu w produkcji addytywnej i jest idealny do prototypów i części funkcjonalnych w lotnictwie i motoryzacji oraz do zastosowań wojskowych. Jest również doskonałym materiałem do produkcji części o złożonej geometrii i precyzji oraz narzędzi produkcyjnych.
- Tytan 6Al-4V klasy 23 to biokompatybilny stop powszechnie stosowany do produkcji implantów i protez medycznych.
- Tytan Beta 21S wykazuje wyższą wytrzymałość niż konwencjonalne stopy tytanu, takie jak Ti-6Al-4V, i ma lepszą odporność na utlenianie i pełzanie w porównaniu do konwencjonalnych stopów tytanu, takich jak Ti-15V-3Cr. Tytan klasy 21 ma jeden z najniższych poziomów wydajności wychwytu wodoru wśród wszystkich stopów tytanu. Jest idealnym kandydatem do implantów ortopedycznych i zastosowań w silnikach lotniczych. Beta tytan jest szeroko stosowany w ortodoncji.
- Cp-Ti (czysty tytan) klasy 1, 2 jest szeroko stosowany w medycynie w szerokim zakresie zastosowań ze względu na biozgodność tytanu z ciałem człowieka.
- TA15 to stop tytanu zbliżony do alfa z dodatkami aluminium i cyrkonu. Wysoka wytrzymałość adekwatna komponentów wykonanych z TA15 w połączeniu z ich wysoką nośnością i odpornością na temperaturę umożliwia ich stosowanie w ciężkich komponentach w budowie samolotów i silników.
- Technologia Carpentera : TI 6AL-4V ELI
- IperionX: poddany recyklingowi Ti
- Dodatek 6K: Ti6Al4V
- Sandvik : Osprey TI-6AL-4V Gr.5 i Gr.23
- GKN : CPTi – Gr.1 i Gr.2, Ti64 – Gr.5 i Gr.23, Ti6242, Ti5553, Beta 21S
- AstroAlloys : TruForm Ti-6Al-4V Gr.5 i Gr.23, Ti-48Al-2Nb-2Cr, Ti-6Al-2Sn-4Zr-2Mo
- Tekna : gruboziarniste proszki Ti64 i Ti64
- Firma Restor3d otrzyma w 2023 r. zgodę na produkcję pierwszego w pełni metalowego (tytanowego) narzędzia drukowanego w technologii 3D, dostosowanego do potrzeb konkretnego pacjenta, służącego do endoprotezoplastyki stawu skokowego.
- Firma SurGenTec w 2023 roku otrzyma zgodę na wprowadzenie do obrotu swojego drukowanego w 3D tylnego systemu stabilizacji stawów krzyżowo-biodrowych TiLink-P, wykonanego z tytanu.
- Firma FloSpin e w 2023 roku otrzymała od FDA zgodę na drukowany w technologii 3D implant służący do podtrzymywania kręgosłupa, zwany Tri-Largo Cervical Interbody Cage System.
- Firma Eminent Spine otrzymała w 2023 roku aprobatę FDA dla swojego systemu 3D Cervical Interbody Fusion System, składającego się z elementów z tytanu drukowanych w technologii 3D .
- Firma ChoiceSpine otrzymała w 2023 r. aprobatę FDA dla swojego systemu dystanserów szyjnych Blackhawk Ti, drukowanych w technologii 3D z tytanu.
- Firma CoreLink otrzyma w 2023 r. zgodę FDA na swój system do zespolenia stawów krzyżowo-biodrowych Siber Ti, składający się z porowatych, pokrytych nanopowierzchnią implantów tytanowych drukowanych w technologii 3D.
- Na początku tego roku firma Silca zaprezentowała swoją najnowszą linię produktów drukowanych w technologii 3D, obejmującą serię haków przerzutki wykonanych z tytanu .
- Verve Cycling i Metron Additive Manufacturing wprowadziły na rynek korbę wykonaną w technologii druku 3D z tytanu o nazwie InfoCrank 3D Ti .
- Firma Moots wprowadziła na rynek nowe, drukowane w technologii 3D tytanowe haki i akcesoria do swojego nowego roweru szutrowego Routt CRD .
- Firma Cane Creek wprowadziła na rynek nowe korby Electric Wings wykonane z tytanu, drukowane w technologii 3D , które są tak lekkie jak korby karbonowe, ale tak wytrzymałe jak korby aluminiowe – twierdzi firma.
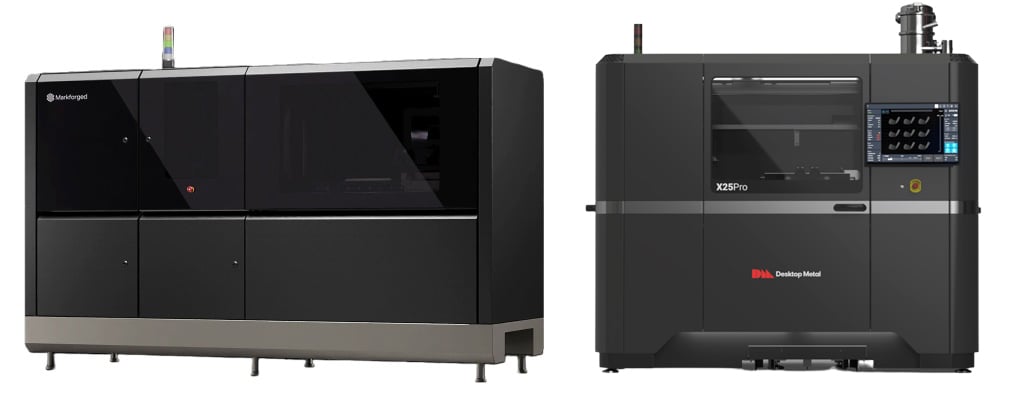
Drukarki do metalu z funkcją druku strumieniowego i tytanu
Drukarki do modelowania metodą osadzania topionego materiału (FDM) i wytłaczania z możliwością obróbki tytanu
Odblokowanie druku 3D z tytanu
Poznaj swój tytan

Czysty tytan nie jest zwykle używany w zastosowaniach inżynieryjnych, podczas gdy jest powszechny na rynku biomedycznym w przypadku części, takich jak implanty kolan i bioder. Stopy na bazie tytanu – kontrolowane mieszanki składników metalowych, które zapewniają określone adekwatności mechaniczne – są używane w szerokim zakresie branż, które muszą osiągnąć bardzo określone adekwatności części. Dostawcy materiałów metalowych, którzy od dawna dostarczają producentom tytan do odlewania, oferują teraz proszki tytanowe opracowane specjalnie do produkcji addytywnej.
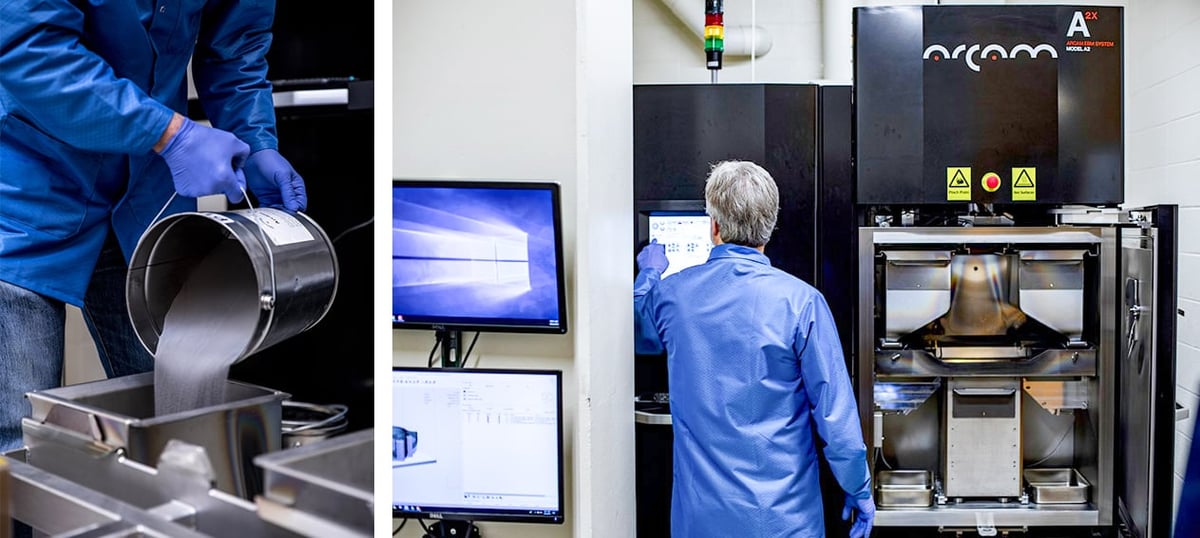
Tytan do produkcji addytywnej
Dostawcy tytanu
Producenci materiałów oferują szeroką gamę tytanu i stopów tytanu specjalnie opracowanych do druku 3D, o różnych rozmiarach cząstek i czystości, w tym:
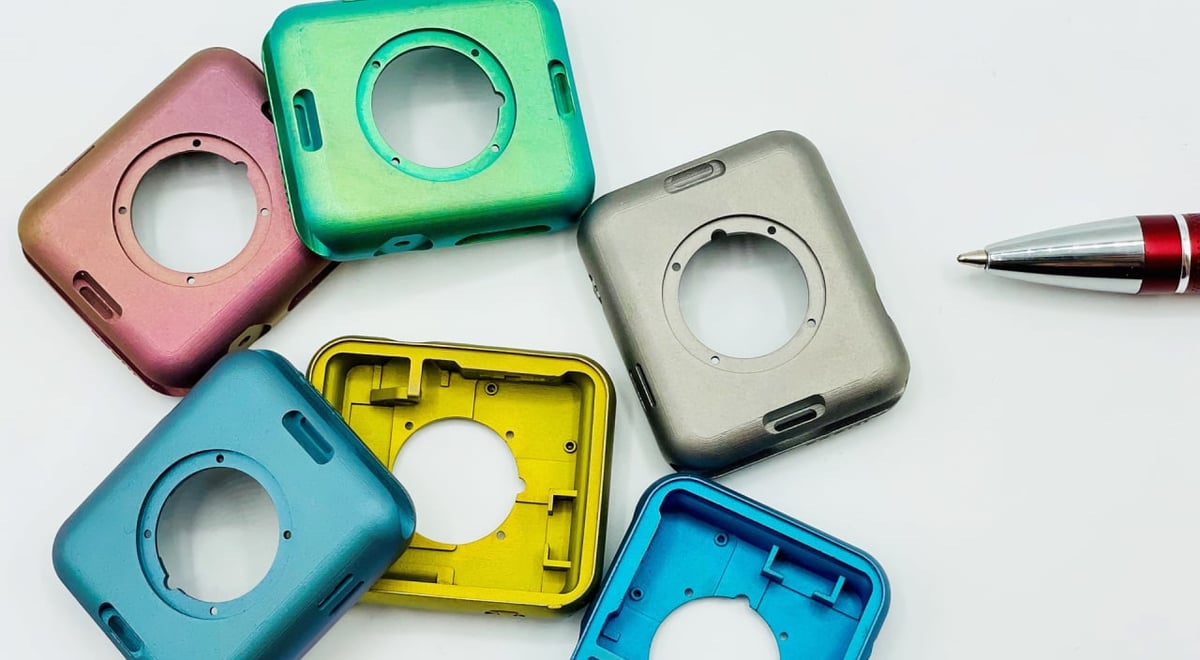
Ostatnio największą nowiną w druku 3D z tytanu jest
zgłoszone zastosowanie w Apple najnowszego iWatcha. Według niepotwierdzonego raportu
Ming-Chi Kuo , analityka usług finansowych, który zbiera informacje od swoich kontaktów w azjatyckim łańcuchu dostaw Apple, gigant technologiczny włączy części z tytanu drukowane w 3D przez Bright Laser Technologies (BLT) do swojego Apple Watch Series 10, począwszy od drugiej połowy 2024 roku. Kuo mówi, iż Apple i BLT eksperymentują z drukiem 3D z tytanu od lat, aby usprawnić ten proces.
BLT nie tylko produkuje szeroką gamę drukarek 3D wykorzystujących technologię laserowego stapiania proszków (LPBF), ale oferuje również usługi produkcyjne.
Kto jeszcze drukuje w 3D z tytanu? To szeroka grupa producentów produkujących wszystko, od urządzeń medycznych i sprzętu wojskowego po rowery o wysokiej wydajności i elektronikę użytkową. Wszystkich ich łączy chęć dostarczenia lekkiego i wytrzymałego produktu o innowacyjnym, często niestandardowym wzornictwie.Odblokowanie druku 3D z tytanu
Implanty medyczne i stomatologiczne

Liczba zatwierdzonych przez amerykańską Agencję ds. Żywności i Leków (FDA) implantów chirurgicznych wykonanych w technologii druku 3D z tytanu stale rośnie, ponieważ producenci sprzętu medycznego coraz częściej stosują produkcję addytywną.
W branży medycznej implanty tytanowe drukowane w technologii 3D odnoszą sukcesy w zastosowaniach związanych z kręgosłupem, biodrami, kolanami i kończynami ze względu na wrodzoną biokompatybilność tego metalu i dobre adekwatności mechaniczne w połączeniu z możliwością drukowania w technologii 3D do tworzenia porowatych struktur — co umożliwia integrację z kością — i masową personalizację w celu uzyskania lepszych wyników leczenia pacjentów.
Implanty tytanowe drukowane w technologii 3D zyskują zarówno na akceptacji regulacyjnej, jak i na popycie. Ponieważ większość implantów medycznych jest produkowana w celu objęcia nimi dużych grup osób z tym samym schorzeniem, nie są one idealnym rozwiązaniem dla wszystkich. Osoby cierpiące na rzadkie schorzenia są często pomijane. Teraz, dzięki drukowi 3D, możliwe jest wytwarzanie implantów zaprojektowanych wyłącznie dla poszczególnych pacjentów.
Nowojorski Hospital for Special Surgery (HSS) poinformował wcześniej w tym roku, iż drukuje w technologii 3D specjalnie wykonane tytanowe protezy stawów w przypadku bardzo złożonych przypadków, w których standardowy implant nie zadziałałby. HSS był pierwszym szpitalem w USA, w którym zainstalowano druk 3D.
W 2023 roku chirurg w Anglii wykonał cztery operacje nadgarstka tego samego dnia, aby skorygować deformację wcześniej złamanych kości nadgarstka dzięki drukowanych w technologii 3D płytek tytanowych dostosowanych do potrzeb pacjenta . „Po zakończeniu tego procesu planowania, spersonalizowana płytka jest drukowana przy użyciu sproszkowanego tytanu, a następnie testowana, wysyłana do Wielkiej Brytanii i sterylizowana w szpitalu powiatowym, gotowa do operacji” — mówi dr Akshay Malhotra, konsultant chirurg ortopedyczny i kierownik kliniczny ds. chirurgii ręki i nadgarstka w University Hospitals of North Midlands.
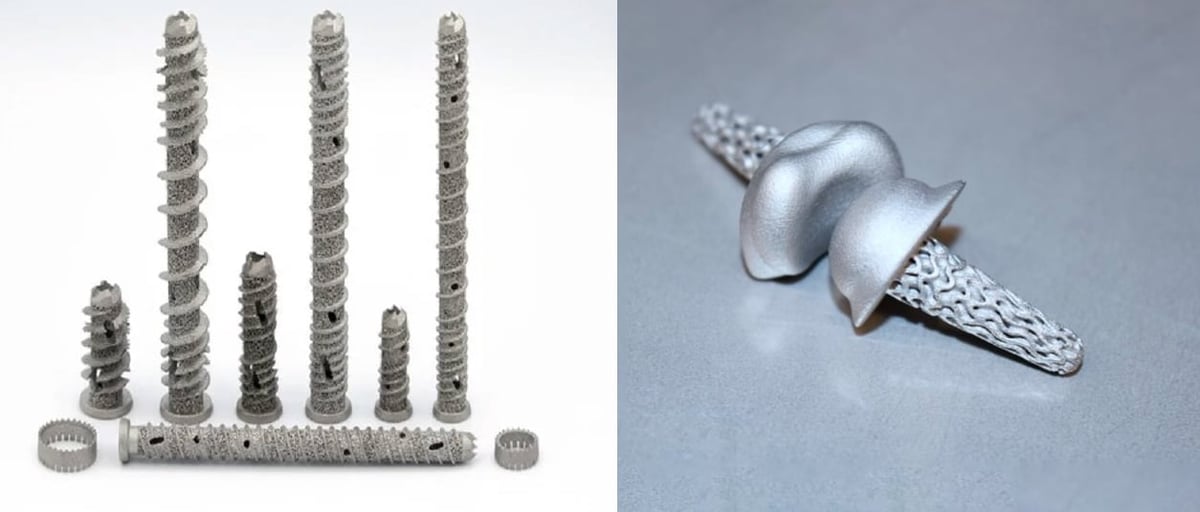
W 2022 roku lekarze ze szpitali Manipal w Indiach, którym przedstawiono pacjenta z chorobą nowotworową, którego guz niszczył klatkę piersiową, zwrócili się w stronę tytanu drukowanego w technologii 3D. Ogólnie rzecz biorąc, implanty tej wielkości są o wiele za ciężkie, aby ludzkie ciało mogło je udźwignąć, ale ze względu na lekkość i wysoką wytrzymałość tytanu, można było wydrukować w technologii 3D implant dostosowany do konkretnego pacjenta, który ważył mniej niż 250 gramów. Dzięki sukcesowi implantu drukowanego w technologii 3D pacjent w pełni wyzdrowiał i mógł wrócić do normalnego życia bez konieczności korzystania z zewnętrznych maszyn wspomagających oddychanie.
W próbie operacji wymiany kości skokowej z wykorzystaniem kości skokowych z tytanu drukowanych w technologii 3D, pacjenci zgłaszali pozytywne wyniki. Wymiana kości oznaczała, iż pacjenci nie musieli przechodzić całkowitej wymiany stawu skokowego. Kości skokowe to bardzo specyficzne dla pacjenta cechy anatomiczne, wymagające unikalnie zaprojektowanej części 3D na podstawie danych z tomografii komputerowej pacjenta.
W 2023 roku amerykańska Agencja ds. Żywności i Leków (FDA) wydała znaczną liczbę zatwierdzeń dla implantów tytanowych drukowanych w technologii 3D, obejmujących głównie implanty kręgosłupa.
Odblokowanie druku 3D z tytanu
Lotnictwo i kosmonautyka

W przemyśle lotniczym i kosmicznym kilka części produkowanych metodą addytywną na bazie tytanu jest w tej chwili wykorzystywanych komercyjnie i wojskowo, a wiele innych prototypów jest w trakcie opracowywania w celu uzyskania certyfikatu FAA. Drukowany w 3D tytan jest ceniony za niski współczynnik „buy-to-fly” — termin lotniczy odnoszący się do zależności między masą początkowego materiału a masą drukowanej części.
Kilku producentów kontraktowych specjalizujących się w rynkach lotnictwa i obronności, przemysłu kosmicznego i kosmicznego, np. Primus Aerospace, StarHagen Aerospace i Zeda, zainwestowało w drukarki 3D umożliwiające produkcję elementów tytanowych zarówno na potrzeby prototypów, jak i gotowych części.
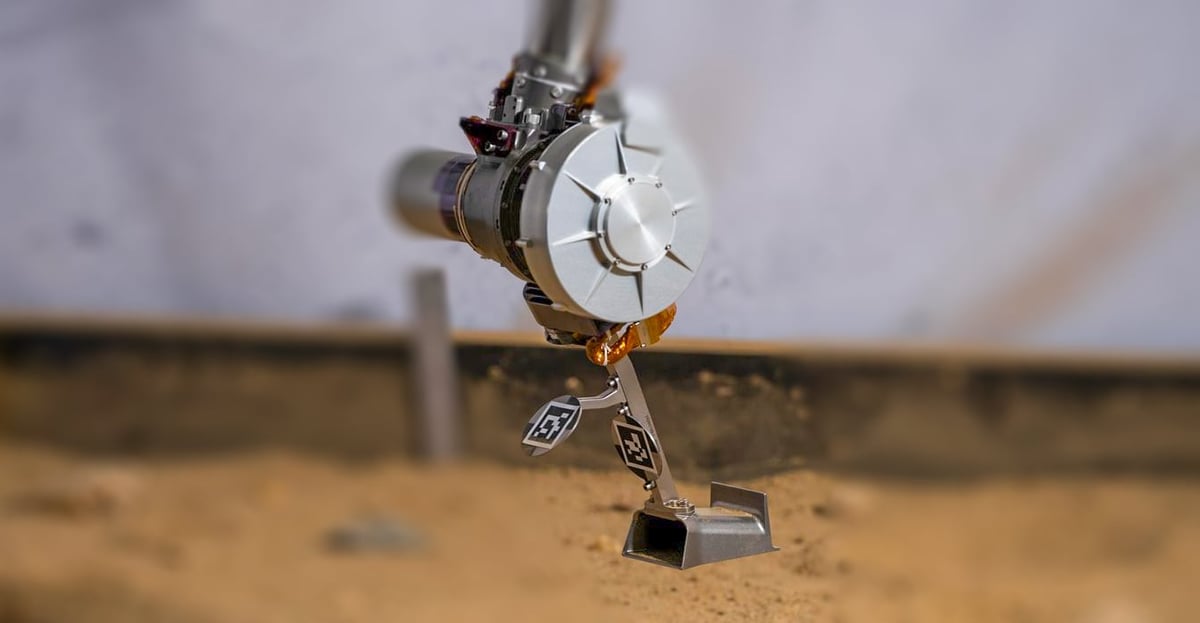
Odblokowanie druku 3D z tytanu
Kolarstwo i produkty konsumenckie

Drukowany w 3D tytan jest dziś niemal powszechny w rowerach o wysokiej wydajności, gdzie liczy się każda uncja wagi, a wysoka wytrzymałość jest najważniejsza. Tytan, stosowany w korbach, uchwytach hamulców, mostkach, hakach przerzutki, a choćby pełnych ramach, okazuje się tak wytrzymały jak aluminium i tak lekki jak włókno węglowe, bez wyzwań związanych ze zrównoważonym rozwojem włókien węglowych.
Niedawno producent rowerów Ribble wypuścił rower Allroad Ti z ramą drukowaną w technologii 3D, która — jak twierdzi firma — „umożliwia nam manualne wytwarzanie rurek tytanowych, które są znacznie bardziej zaawansowane pod względem wydajności aerodynamicznej niż standardowe okrągłe rurki stosowane w typowych ramach tytanowych”. Druk 3D pozwolił również firmie Ribble wyeliminować spoiny, umożliwić niewidoczne prowadzenie kabli i konsolidację części.
Nowojorska firma No. 22 Bicycle Company, która od lat specjalizuje się w rowerach tytanowych, zadebiutowała w sierpniu, Reactor Aero , który integruje kilka drukowanych w 3D komponentów tytanowych i zostanie oficjalnie wprowadzony na rynek w 2025 roku. W komunikacie prasowym Bryce Gracey, współzałożyciel No.22, powiedział: „Drukowany w 3D tytan ma fenomenalne adekwatności strukturalne. Możliwość drukowania wewnętrznych struktur podporowych w dowolnym miejscu ramy daje nam poziom kontroli nad jakością jazdy, który nie był wcześniej możliwy”.
Mówiąc o pełnych ramach, producent rowerów Angel Cycle Works 3D drukuje pełną tytanową ramę w jednym lekkim elemencie, co pozwala zaoszczędzić krytyczne sekundy czasu wyścigowego i umożliwia nową geometrię projektu, mówi firma. Jej nowy hiperrower, zwany Heaven, jest o 400 g lżejszy od poprzednich wersji. Inna pełna tytanowa rama pochodzi od Pilota, wprowadzonego na rynek w tym roku, nazywa się Pilot Seiren. Ten rower szosowy ma ramę, która jest w całości drukowana w 3D (w trzech częściach) z tytanu. Firma twierdzi, iż drukowany w 3D tytan umożliwia jej dopasowanie rowerów do preferencji kolarzy, a ramy nie wymagają żadnej farby ani powłoki.
Carbon Wasp szczegółowo opisał, dlaczego porzucił aluminium i włókno węglowe, a w przypadku swojego najnowszego ramienia korby na rynku wtórnym zwrócił się w stronę tytanu drukowanego w technologii 3D: „Wymyśliliśmy mnóstwo kreatywnych sposobów na zamocowanie korb na osi skrzyni biegów bez ściskania włókna węglowego, ale zawsze musieliśmy uwzględnić jakieś metalowe wkładki…, ale mieliśmy mnóstwo problemów z łączeniem wstawek z włóknem węglowym”. Po kilku prototypach Carbon Wasp odkrył, iż tytanowe korby drukowane w technologii 3D wypełnione kratownicą są tak lekkie jak włókno węglowe, ale bardziej wytrzymałe w obszarze, który jest bardzo narażony na uderzenia. „Wciąż uważamy, iż włókno węglowe jest najlepszym materiałem do wielu innych zastosowań, w tym do ram, … ale już pracujemy nad innymi częściami tytanowymi”.
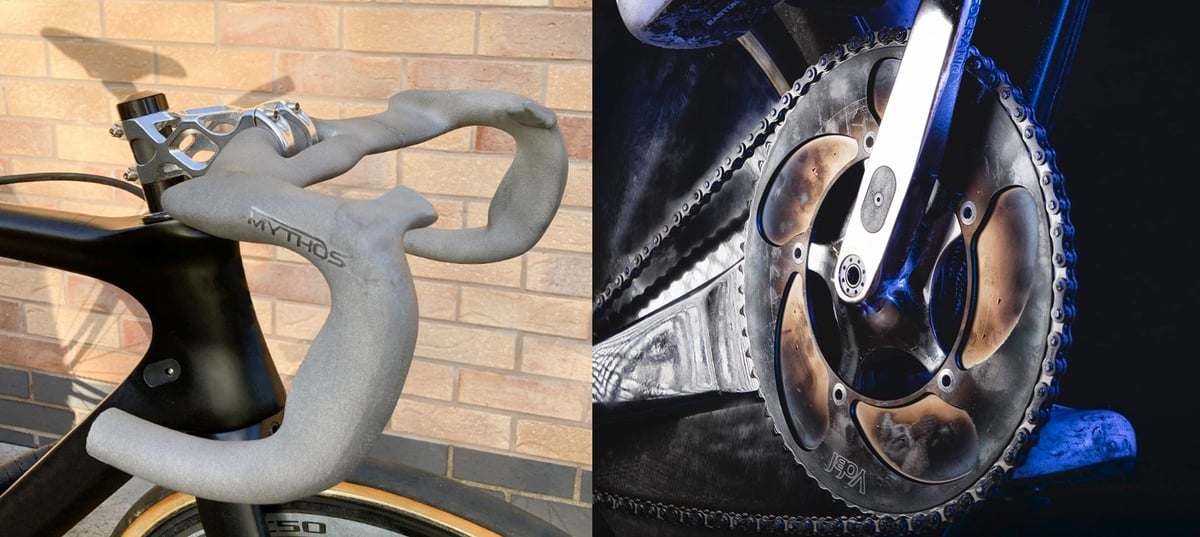
„Proces drukowania umożliwia cieńsze ścianki, co prowadzi do lżejszej i mocniejszej ramy bez punktów naprężeń” – powiedział Tim Blankers z Pilot na stronie internetowej Road.cc Cycling. „Waga ramy wynosi nieco ponad kilogram. Pilot może również dodać materiał w miejscach, w których wymagana jest sztywność, aby zoptymalizować transmisję mocy”.
Chiński producent rowerów Hanglun twierdzi, iż zwiększa wykorzystanie druku 3D z tytanu w 2024 r. „Planujemy wykorzystać technologię druku 3D do produkcji ram i części rowerowych z tytanu, których roczna produkcja wyniesie ponad 50 000 sztuk” — poinformowała firma. Części zostaną zastosowane w różnych modelach rowerów, co ma na celu zapewnienie klientom bardziej wytrzymałych, lżejszych i trwalszych produktów rowerowych z tytanu.
Na rynku dostępnych jest wiele elementów tytanowych drukowanych w technologii 3D przeznaczonych do kolarstwa:
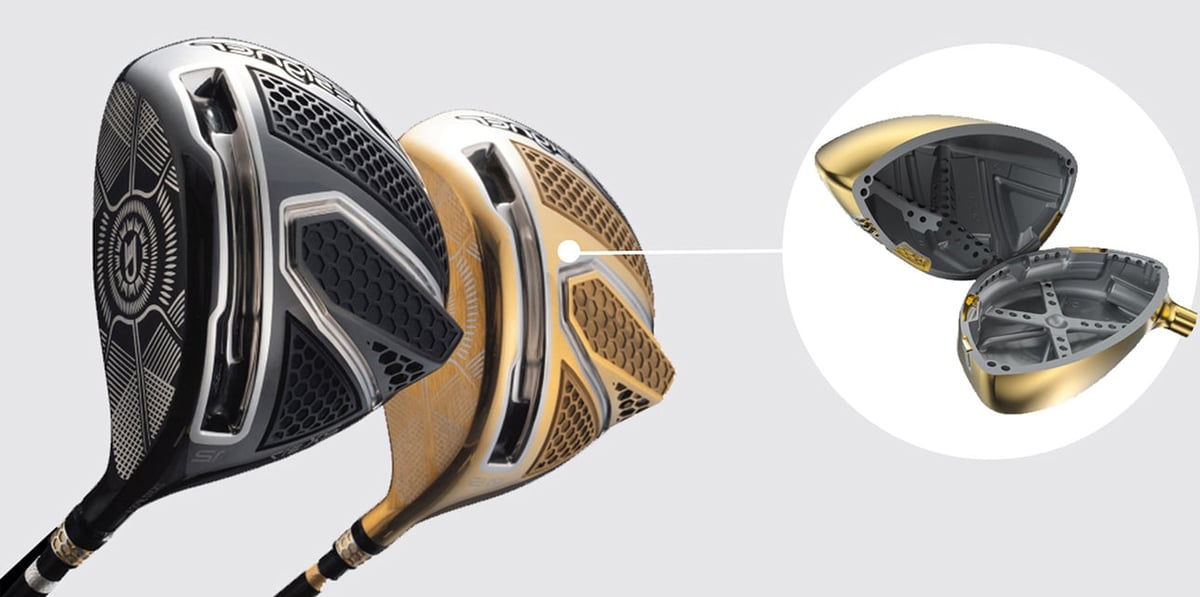
Designer, japońska marka golfowa, wypuściła na rynek kij golfowy z tytanu drukowany w technologii 3D na początku tego roku, jak twierdzi, oferujący golfistom większy dystans, dokładność, stabilność i większą wyrozumiałość. Tytanowa główka kija jest produkowana przy użyciu drukarki 3D z podwójnym laserem do łączenia proszków Farsoon Technologies.Odblokowanie druku 3D z tytanu
Produkcja
Zwracając się do tytanu drukowanego w technologii 3D z zupełnie innego powodu, producent półprzewodników ASML ma teraz swoje tytanowe tacki nośne (używane do produkcji płytek) drukowane w technologii 3D zamiast kute, co pozwala zaoszczędzić 64% surowców i jest dostarczane szybciej. Norsk Titanium, firma zajmująca się produkcją addytywną metali, wykorzystała platformę Directed Energy Deposition (DED), Norsk drukuje 80-kilogramowe (około 176 funtów) preformy o kształcie zbliżonym do netto — używane do produkcji płytek półprzewodnikowych — z Ti64.
Norsk współpracował z holenderskim partnerem Hittech Group, aby opracować preformę, która według Norsk jest używana w systemie litograficznym ASML. ASML, również z siedzibą w Holandii, jest jedną z najczęściej omawianych firm na świecie w kontekście niedoborów chipów w ciągu ostatnich kilku lat. W szczególności ASML jest najbardziej znana z produkcji jedynych na świecie maszyn do fotolitografii w ekstremalnym ultrafiolecie (EUV).
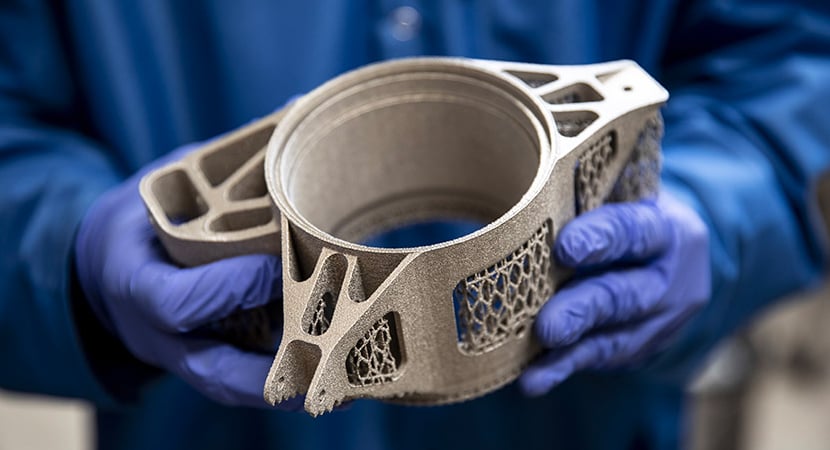
Nawet US Navy zwraca się w stronę tytanu drukowanego w technologii 3D, aby zaoszczędzić czas i pieniądze oraz wyeliminować zależność od zagranicznego łańcucha dostaw. Nie mając krajowych zdolności produkcyjnych do produkcji dużych odlewów tytanowych wymaganych do wysokowydajnych pomp odśrodkowych, marynarka wojenna walczy z długimi terminami realizacji i łańcuchem dostaw, który wykorzystuje drogie i wysokoemisyjne surowce tytanowe. Jednak wkrótce, dzięki nowym krajowym partnerom IperionX w zakresie proszków tytanowych z recyklingu i Carver Pump w zakresie produkcji addytywnej, marynarka wojenna zyska możliwość znacznego skrócenia terminów realizacji kluczowych części, zwiększenia dostępności sprzętu i zrównoważonego powrotu do kraju kluczowego amerykańskiego łańcucha dostaw tytanu.Odblokowanie druku 3D z tytanu
Produkty precyzyjne, elektronika i biżuteria

Druk 3D pozwala na tworzenie niezwykle cienkościennych, misternych i skomplikowanych części tytanowych. Dlatego wykorzystuje się ją do produkcji kopert zegarków, np. zegarków Panerai i Holthinrichs (przedstawionych powyżej).
W 2023 roku producent telefonów Honor wprowadził na rynek nowy składany Magic V2 z tytanową pokrywą zawiasu wydrukowaną w technologii 3D, która jest lżejsza od poprzedniej wersji aluminiowej i o 150% mocniejsza. Firma twierdzi, iż ten mały element tytanowy, który można wydrukować w technologii 3D w dziesiątkach tysięcy, jest kluczem do trwałego i płynnego składania i rozkładania produktu.
O autorze:
Juan C. Colombo-Pulgarín jest inżynierem mechanikiem z tytułem doktora inżynierii materiałowej. Jego badania, w tym „ Beta Titanium Alloys Processed By Laser Powder Bed Fusion: A Review ” i „ Mechanical and Chemical Characterisation of TiN and AlTiSiN Coatings on a LPBF Processed IN718 Substrate ”, ukazały się w różnych czasopismach naukowych.
źródło: all3dp
