Simon Metzner ma problem. Żona narzeka bez przerwy na metalowe opiłki, które przynosi na butach. Co ma jednak zrobić? Są aluminiowe, magnesem nie da się ich zebrać. Za to zawsze może się tłumaczyć, iż na szczęście do domu nie przynosi pracy. Tę, kiedy śpi, przez cały czas wykonuje za niego zautomatyzowana obrabiarka.
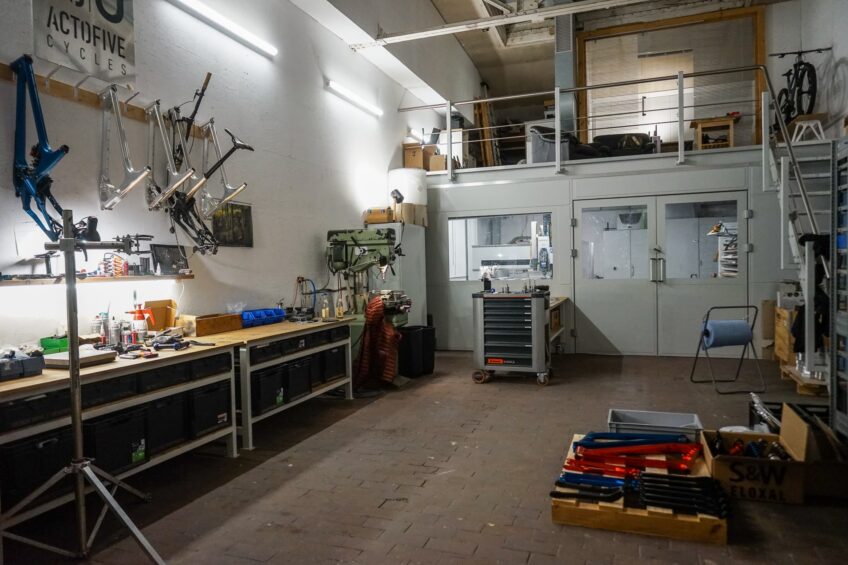
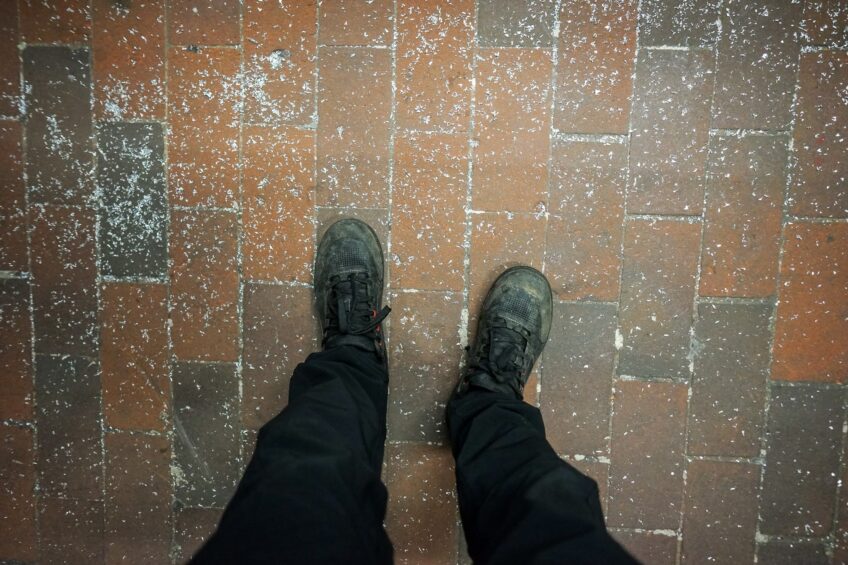
Jesteśmy w niewielkim, wydzielonym warsztacie w jednej z wielu hal produkcyjnych dzielnicy, która nazywa się po prostu drezdeńskimi terenami przemysłowymi (Dresden Industriegelände). W całym mieście praktycznie bez przerwy spotyka się na podobne budynki, w lepszym lub gorszym stanie. To pamiątka dawnej, przemysłowej przeszłości miasta, dziś symbol tego, jak produkcja powraca, choć często w trochę odmienionej postaci. Ten fragment dzielnicy jest jednak wyjątkowy. Kilkaset metrów obok mieści się Beast Components, czarujące części rowerowe z kompozytów, przez ścianę siedzibę miał Sour Bicycles, a przez cały czas ultra lekkie koła buduje Light Wolf Studio.
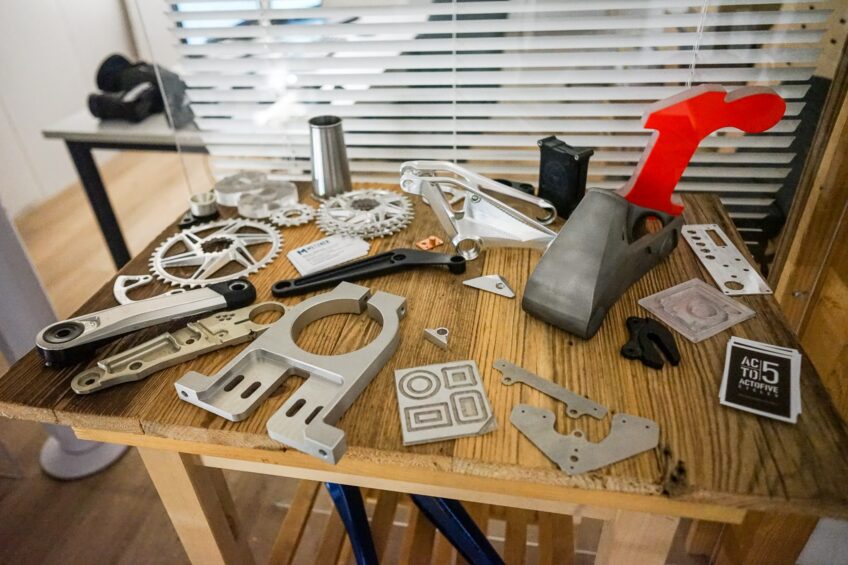
Precyzyjnie rzecz biorąc jesteśmy w firmie Metzner Engineering, Actofive to jej marka. Albo wizytówka, w zależności od punktu widzenia, bo tak naprawdę zajmuje może 80% czasu, ale przynosi tylko 20% zysków. Na sterowanej cyfrowo obrabiarce można w końcu wyprodukować z aluminium niemal wszystko, co wymaga wysokiej precyzji, nie tylko komponenty rowerowe.
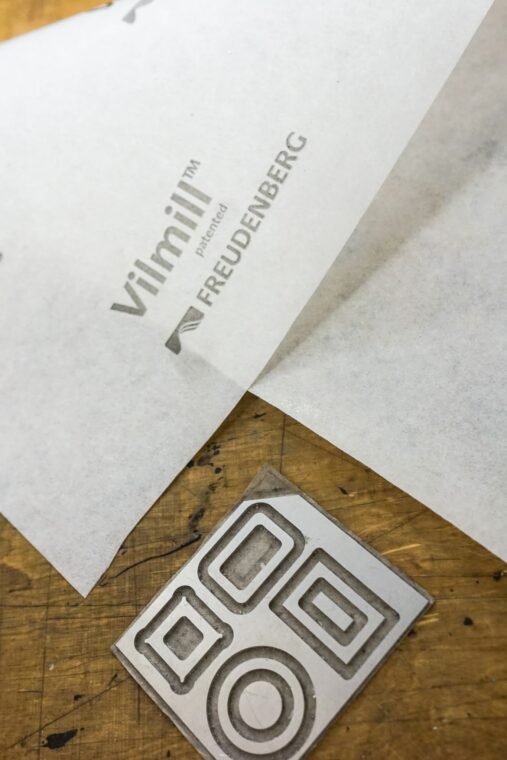
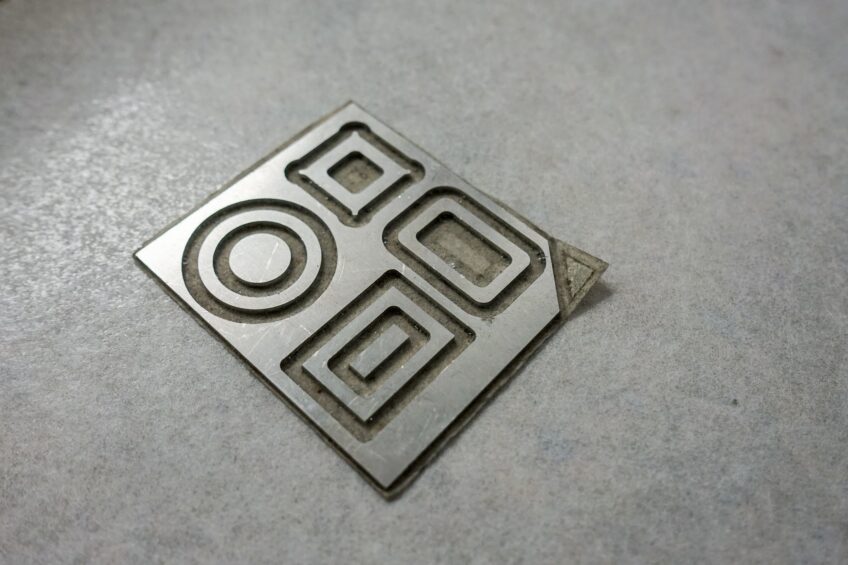
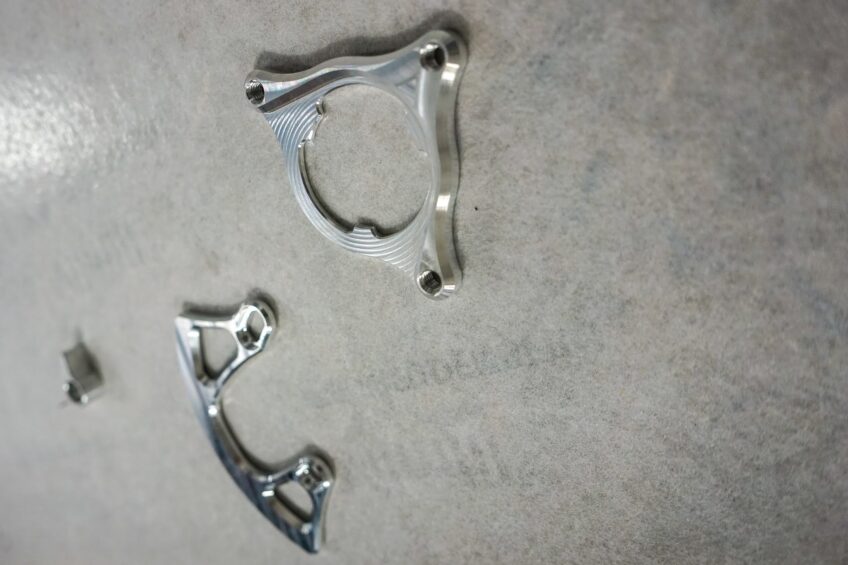
Przypadek
Przypadek albo nie, faktem jest, iż żeby powstały cudeńka Actofive musiała spleść się pasja Simona z historią rodzinną. Metzner Engineering nie miała powstać, zamiast tego miał po ojcu przejąć produkcję i klientów Portatec, firmy specjalizującej się w wytwarzaniu obrabiarek, wykorzystywanych głównie w przemyśle lotniczym. Okazało się, iż jednak „stary” szef i „młody” szef nie są w stanie razem pracować, jedna z obrabiarek trafiła pod nowy dach, by Simon miał już działać „na swoim”. To, iż niejako przy okazji będzie wytwarzać komponenty rowerowe, było dla Simona oczywiste, rowery to była jego prawdziwa pasja. Choć z drugiej strony patrząc na to, jak pracuje, zastanawiałem się, czy to jednak nie sam proces, w którym powstają.
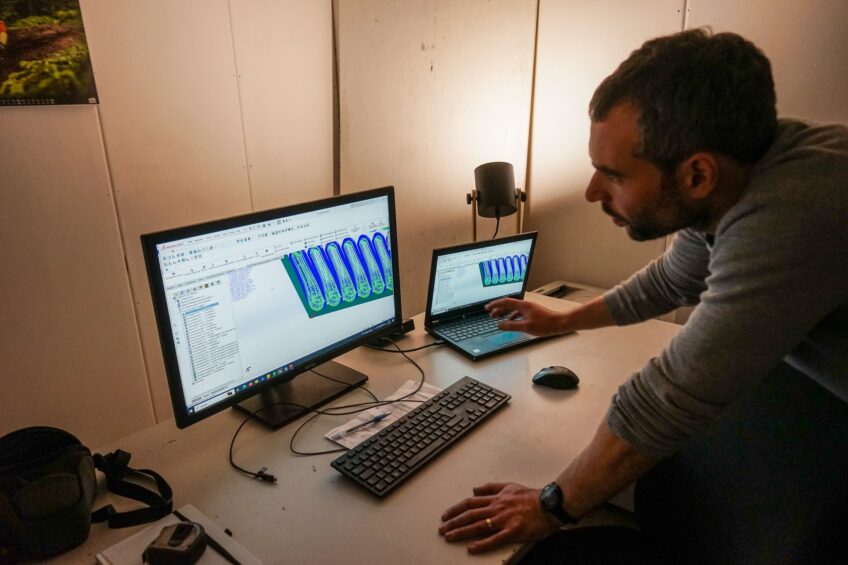
Pięterko
Wszystkie komponenty produkowane przez Metzner Engineering zaczynają życie w ten sam sposób, w komputerze Simona w biurze na górze nad maszyną. Tu tu w programie SolidWorks projektuje wszystkie części i planuje etapy wytwarzania. Już na tym etapie dzięki środowisku 3D widać, jak będą wyglądać i sprawdzać dzięki wirtualnych testów. Co nie oznacza, iż jest to proste, diabeł jak zwykle tkwi w szczegółach. A te sprowadzają się np. do odpowiednich narzędzi, które często powstają na specjalne zamówienie.
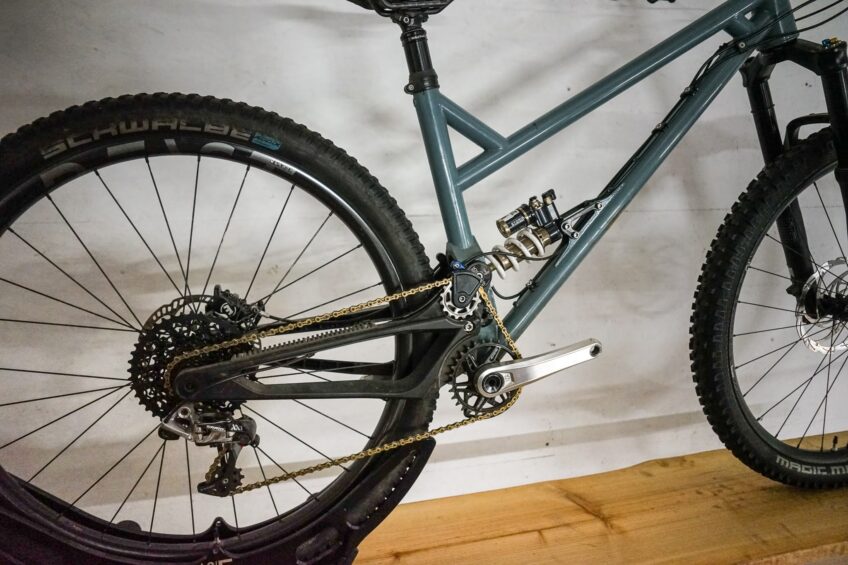
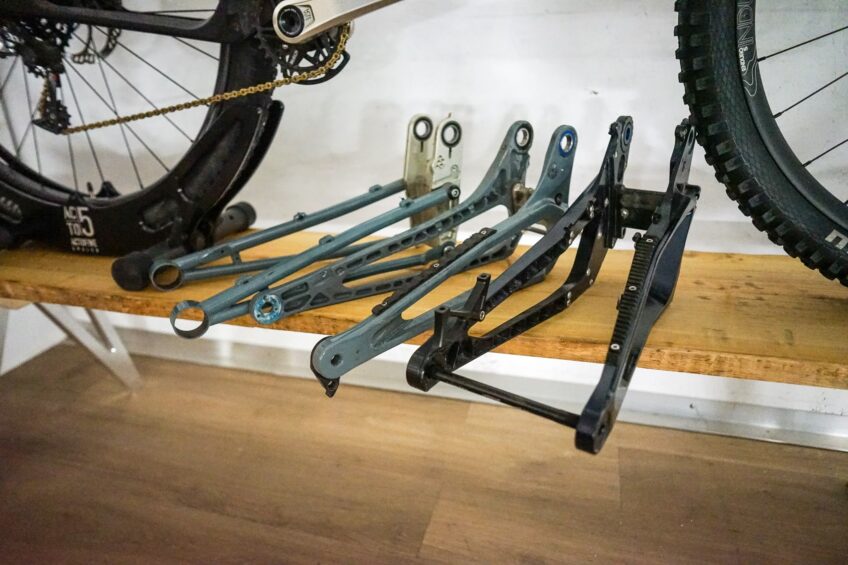
Tuż obok biura stoi pierwszy rower, który stworzył Simon. Miał już to samo zawieszenie, jak późniejsze enduro P-Train z high pivotem, ale samą ramę jeszcze ze stali. Przedni trójkąt wyspawała manufaktura Unique, tył w kolejnych wariacjach to był już Actofive. Od tego się zaczęło.
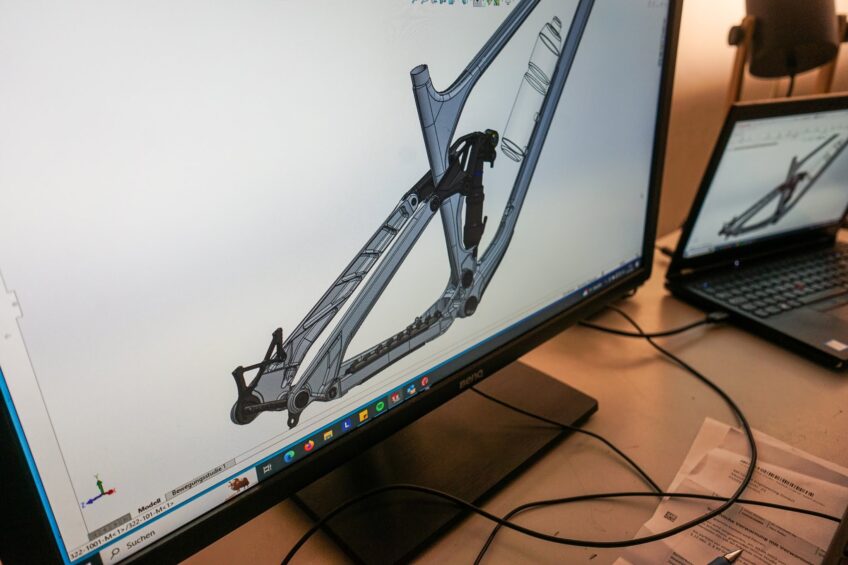
Proces
Z komputera na górze program trafia do centrum sterowania obrabiarką na dole, które ma własną pamięć. Dlaczego? Powód jest prosty, w przypadku przerwania połączenia z komputerem nie ma konieczności zatrzymania produkcji. A sama obrabiarka i jej stół są tak duże, iż swobodnie można zaplanować pracę na 8 godzin do przodu i ta może odbywać się bez udziału człowieka. To nie znaczy, iż bez kontroli, bo Simon cały czas może kontrolować i widzieć urządzenie online. I np. sprawdzić, iż maszyna już kończy.
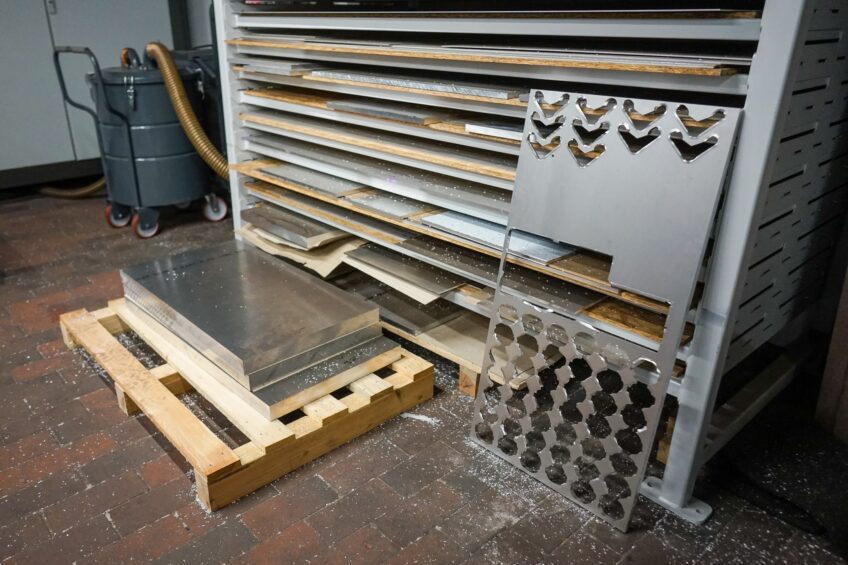
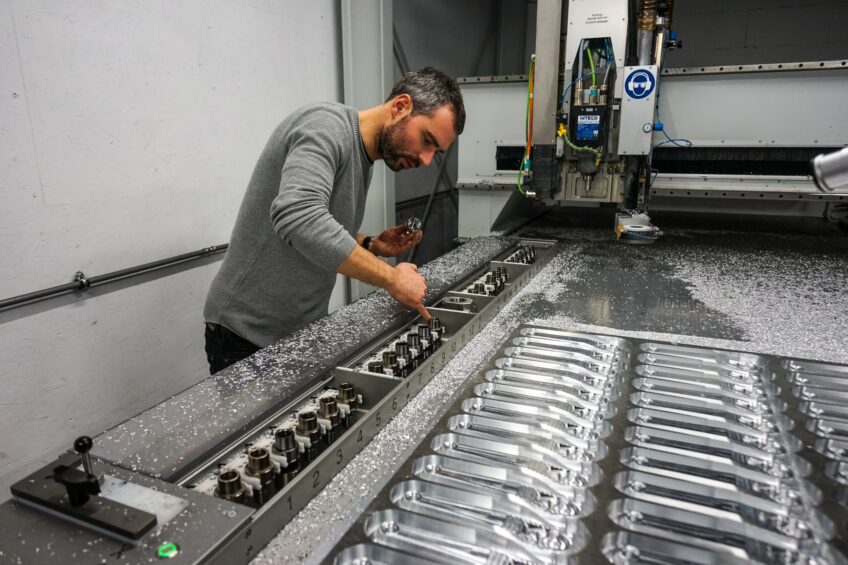
Wszystkie części zaczynają życie w ten sam sposób. To cieńsza lub grubsza płyta aluminium. Standardowe produkty Actofive powstają z tych grubszych, to korby i połówki ramy. Cieńsze płyty zarezerwowane są dla drobiazgów, typu kapsle do sterów czy zębatki. Tu też poces jest odrobinę inny, bo płyta spoczywa na… papierze z klejem Vilmill, który „trzyma” komponenty i chroni stół roboczy. To zresztą także produkt chroniony patentem Portatec.
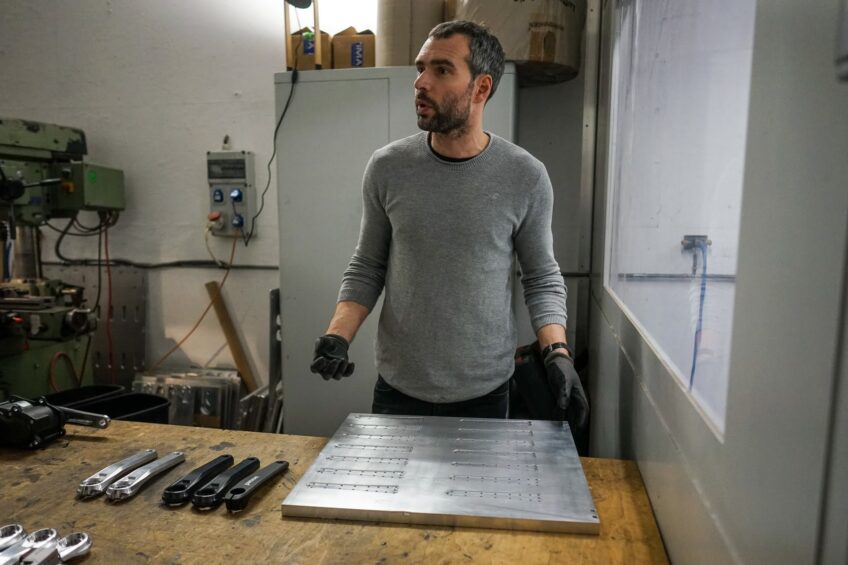
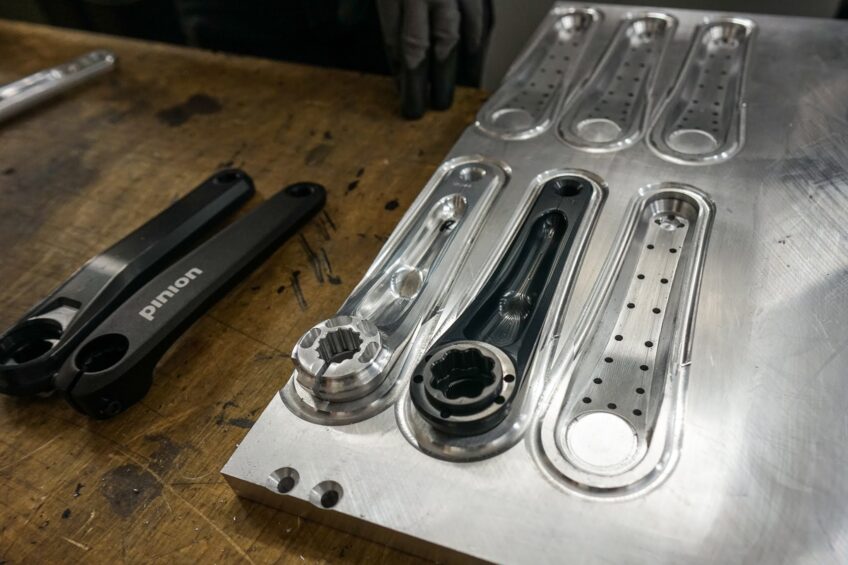
W przypadku korb Actofive czy fragmentów ramy wszystko zaczyna się od grubych i ciężkich aluminiowych płyt, które przenosi się specjalnym dźwigiem, bo to konkretny kawał metalu. W zależności od skomplikowania do uzyskania finalnej postaci kroków produkcji może być więcej, bo dochodzi np. klejenie, ale zawsze są najpierw dwa podstawowe. Najpierw jest obróbka jednej strony „po prostu” z płyty, gdzie wykorzystuje się jak najbardziej ekonomicznie całą dostępną powierzchnię. Co oczywiście trwa wiele godzin, ale na raz powstaje wiele takich samych komponentów, np. 60 ramion korb. Następnie można przystąpić do obróbki drugiej strony, a oswobodzone po pierwszym etapie części są trzymane za pomocą… próżni. Po to w negatywnych formach są otwory. Oczywiście do tego potrzebne jest ciśnienie, którym także można odpowiednio sterować. Sam stół w obrabiarce ma mniejsze strefy, nie trzeba go więc wykorzystywać w całości.
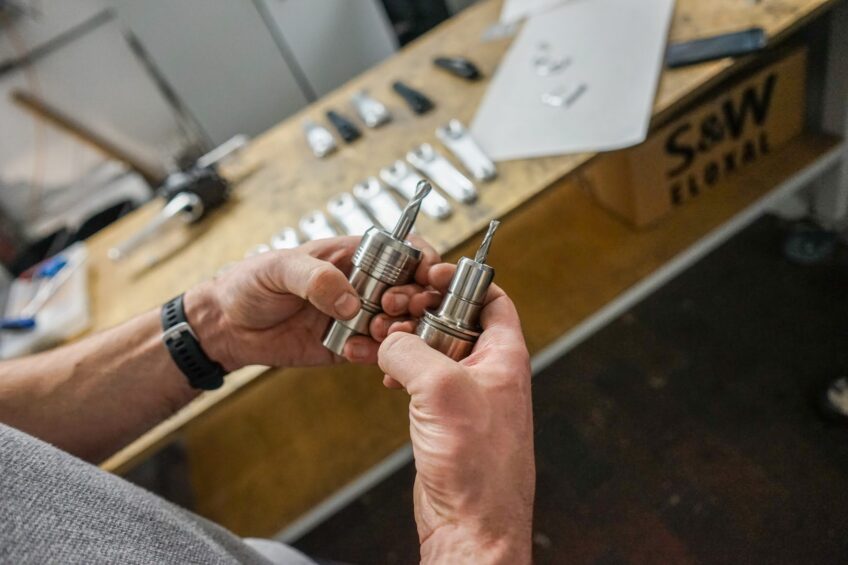
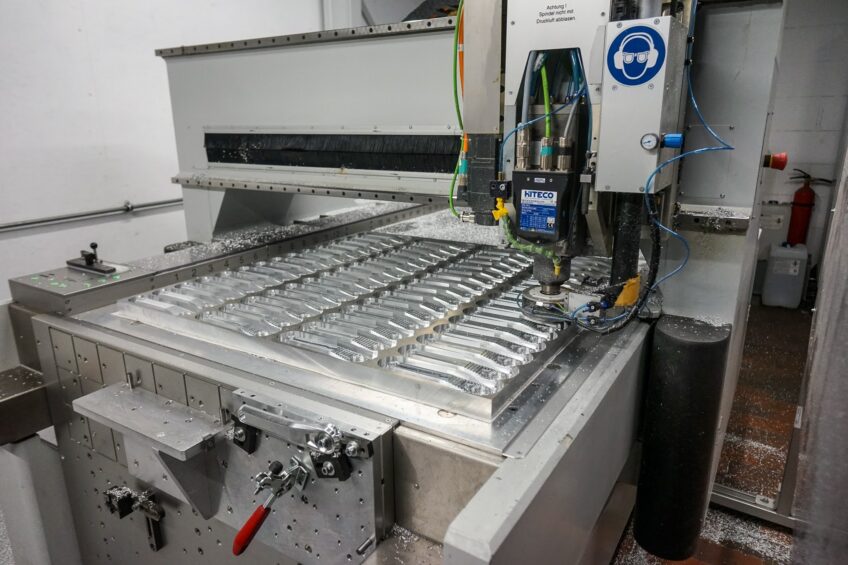
Etapy procesu mogą być dwa, ale może być ich więcej. Rama składa się z większej ilości części, sam trójkąt główny z dwóch. Po obrobieniu obydwu z każdej strony te dopiero są sklejane. Inne komponenty, jak rocker w wahaczu, są sklejane i skręcane.
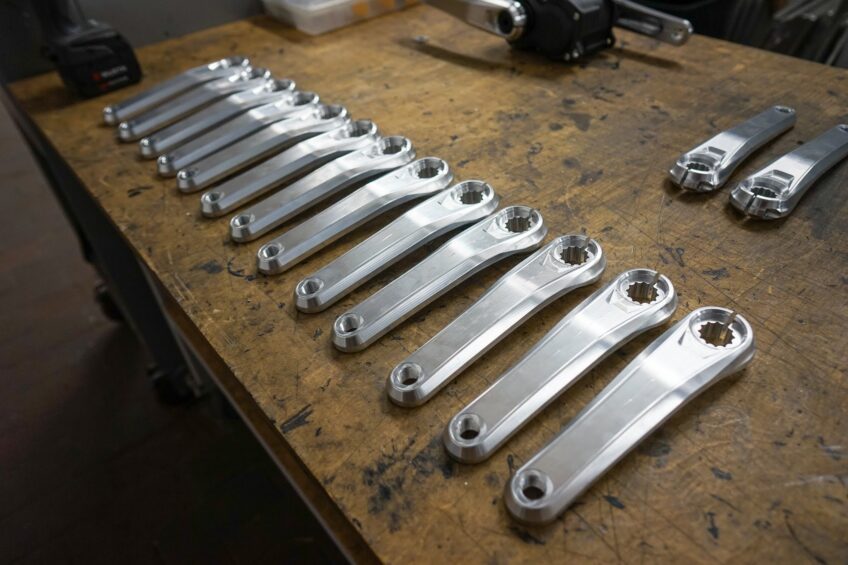
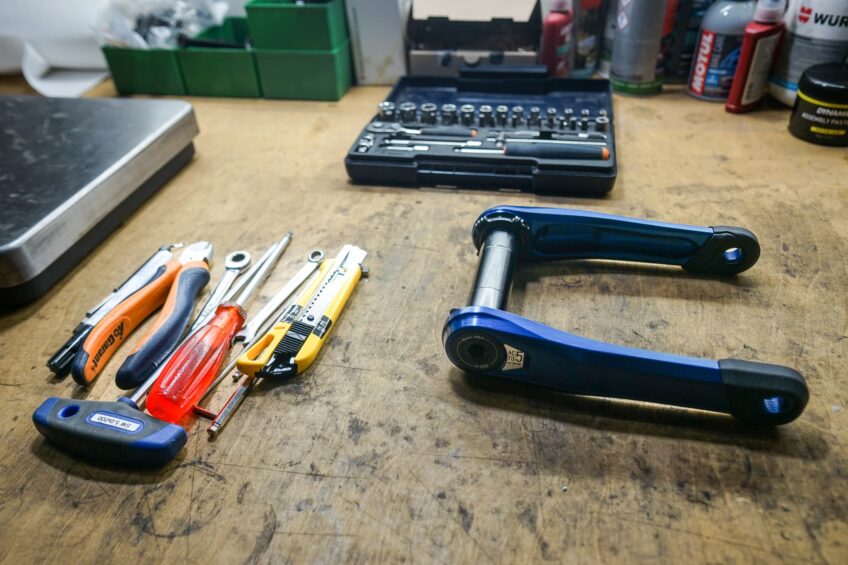
Na końcu jest anodowanie. Tu Simon nie pozostało samowystarczalny, ale myśli i o tym. Na razie części wędrują do różnych zakładów w całych Niemczech, wyspecjalizowanych w uzyskiwaniu różnych kolorów, co także nie jest proste.
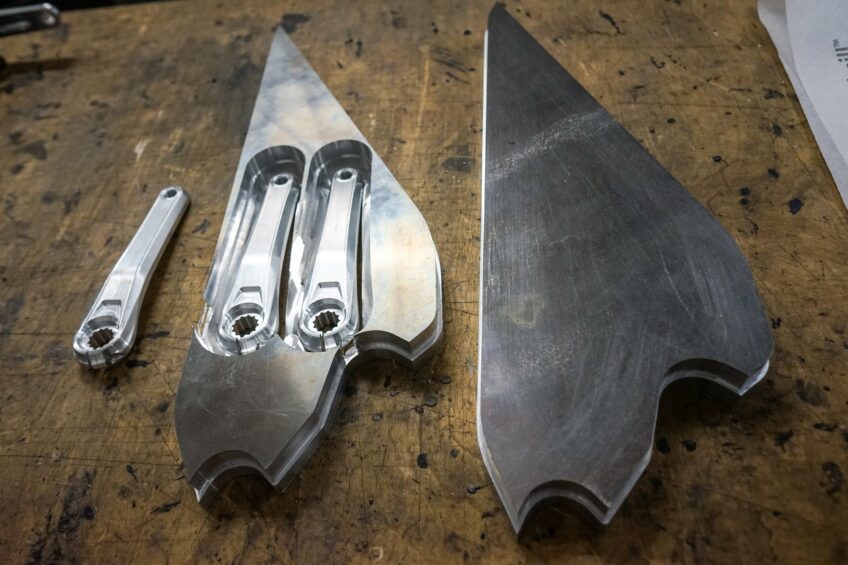
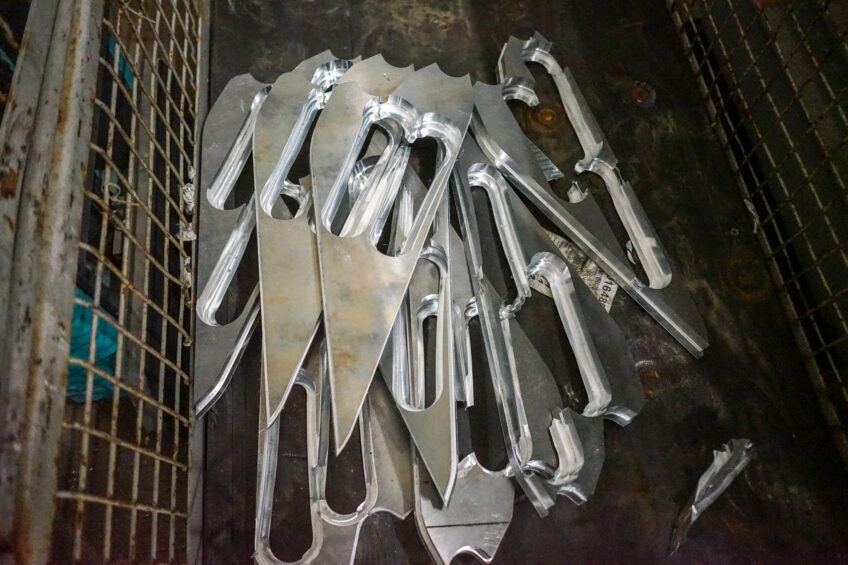
Prototypy
Fakt, iż proces tworzenia komponentów odbywa się w całości na miejscu oznacza także to, iż ewentualne zmiany można wprowadzić błyskawicznie. W ten sposób powstały np. nowe korby Signature w wersji do Piniona – wystarczyło tylko zmienić sposób mocowania w istniejącym modelu. Simon świadomie korzysta do tworzenia prototypów „odpadki” z innych produktów – pozostałe fragmenty płyt. Ba, po stworzeniu wersji w komputerze możliwe jest nie tylko ponowne uruchomienie produkcji, jeżeli tylko pojawi się popyt, a choćby modyfikacje i kolejne warianty, typu inna długość korby. Czy tak w przyszłości będzie wyglądać produkcja zawsze, pod klienta? To już możliwe, wystarczy tylko przekroczyć próg opłacalności, a ten dla technologii takiej jak ta oznacza już setki a nie tysiące komponentów.
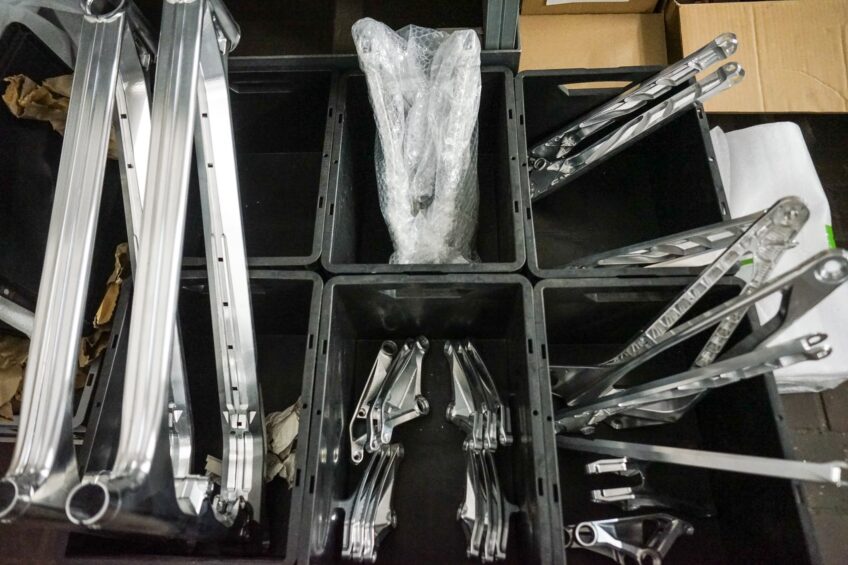
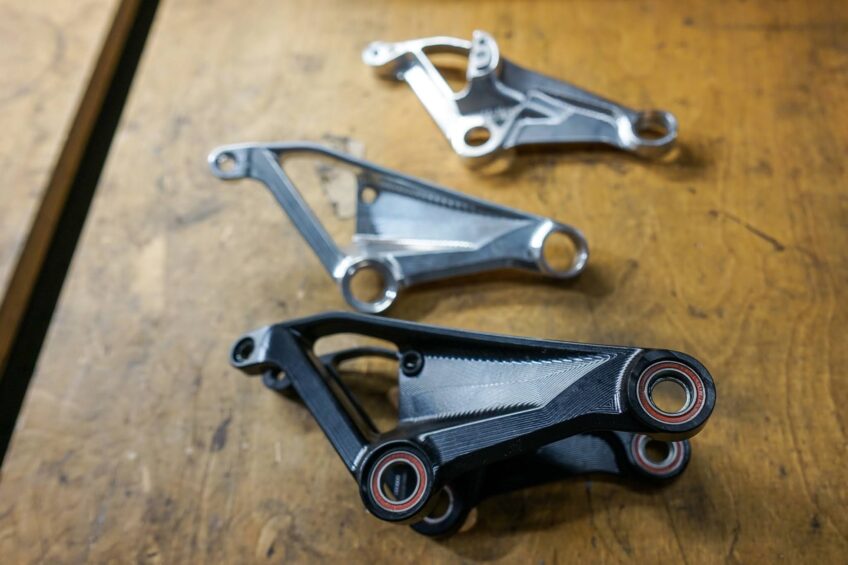
Granice
Na razie trudno przeskoczyć fakt, iż niewielkie serie i produkcja z Niemczech przekładają się na wysokie ceny. Nie zmienia tego wysoki stopień automatyzacji. Dlatego też rowery takie jak Actofive pozostaną w przewidywalnym czasie ekskluzywne. Podstawowy model enduro P-Train to koszt od 12900 Euro za kompletny rower i 6750 Euro za samą ramę. Nowy, ścieżkowy I-Train jest odrobinę tańszy, bo rama kosztuje 5450 Euro. Korby to odpowiednio 799 Euro za Signature z ramionami pustymi w środku i 399 Euro za Signature X, o bardziej tradycyjnej konstrukcji. A granica w górę? Obok pierwszego prototypu P-Train mogłem zobaczyć na miejscu fragment tej ramy wykonany z tytanu, wydrukowany w technice 3D. Teoretycznie rower mógłby być także wykonany z tego materiału. Ktoś zainteresowany? Na wszelki wypadek podaję namiary – actofive.com
Ps na dole widzicie warsztat po ludzkiej zmianie. Obrabiarka CNC przez cały czas robi swoje.
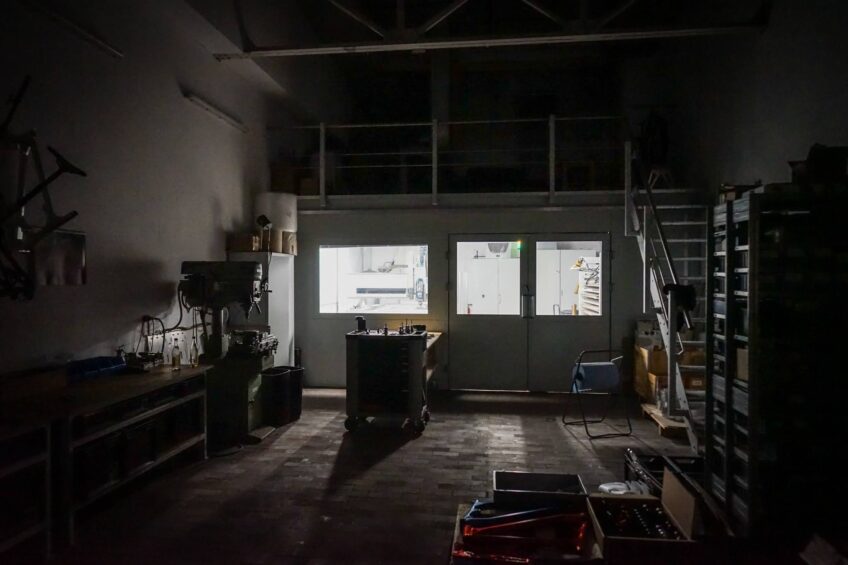