Projektanci i producenci na całym świecie stają się świadomi nowych możliwości, jakie druk 3D może otworzyć dla ich produktów. Chociaż wyłączne wykorzystanie PLA, ABS i materiałów metalicznych nie jest wdrażane poza kontekstem czysto koncepcyjnych kreacji, istnieje wiele przykładów akcesoriów odzieżowych, które mogą być już tworzone przy użyciu drukarek 3D. Jednym z fascynujących przykładów jest niedawny projekt klamer autorstwa Studia MHOX dla czołowego włoskiego projektanta pasków Scunzani.
Tylko dwadzieścia pięknych wzorów z setek generatywnych fenotypów
Ta limitowana seria wykorzystuje niekonwencjonalne “włóknisto-formacyjne wzornictwo”, aby zapewnić odrobinę klasycznej i stylowej estetyki. Istnieje dwadzieścia różnych formacji, które zostały wybrane z setek fenotypów, które zostały wygenerowane na początku. Formacje te mogą być automatycznie dostosowane do indywidualnych potrzeb, aby stać się idealnym dopasowaniem dla wszystkich. Główną zaletą wykorzystania druku 3D do stworzenia tych klamer jest to, iż koszty są znacznie niższe, podczas gdy możliwości personalizacji rosną wykładniczo. Każda klamra jest dostosowana do włoskiej finezji Scunzani i jest unikalna w formie i tworzeniu.

MHOX, specjalistyczne studio, które opracowało projekt tych niesamowitych klamer, aktywnie pracuje nad formacjami perlistymi i włóknistymi. Wiedza ta została wdrożona w innych projektach, takich jak ten wykorzystany w tej masce kolagenowej przedstawionej na zdjęciu lub przy tworzeniu ortez medycznych (drukowanych w 3D niestandardowych podpór dla osób cierpiących na bóle stawów) i odlewów generatywnych.
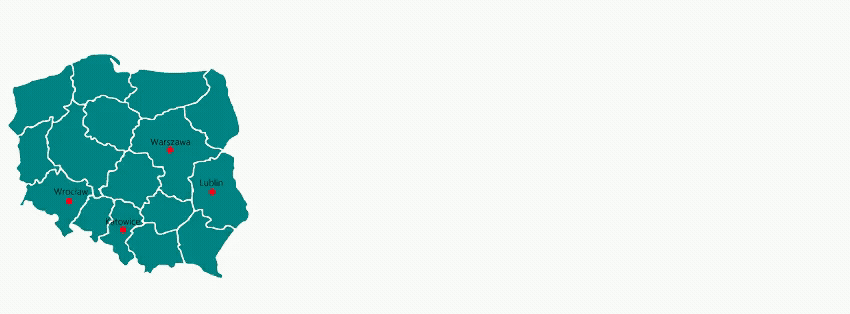
W przypadku obu projektów studio stworzyło obiekty o wysokim poziomie precyzji i możliwości adaptacyjnych, potrzebnych do tego, aby tak abstrakcyjny projekt mógł usadowić się na twarzy lub części ciała danej osoby. Osiąga się to poprzez zeskanowanie ciała osoby, dla której tworzona jest maska lub klamra, a następnie umożliwienie komputerom przeprowadzenia symulacji wzrostu układów włókien i stworzenia modelu 3D. Projektanci mogą zróżnicować efekt końcowy na różne sposoby, a tym samym osiągnąć własne, unikalne podejście artystyczne.

Nowe materiały dla złożonych obiektów
W faktyczny druk 3D tych klamer zaangażowany jest kolejny specjalista w tej dziedzinie. Za “materializację” tak skomplikowanych geometrycznie obiektów odpowiada CRP Group. Firma z Modeny we Włoszech współpracuje ze światowej klasy firmami z branży lotniczej i sportów motorowych i udowodniła swoją zdolność do tworzenia drukowanych w 3D obiektów, które sprawdzają się w najnowocześniejszych implementacjach technologicznych i w bardzo wymagających aplikacjach.
Wykorzystując materiały do produkcji addytywnej Windform do spiekania laserowego, które jest jedną z najbardziej zaawansowanych technologii druku 3D, CRP jest w stanie drukować 3D obiekty, które są mocne i niezawodne. Części te mogą być dalej obrabiane przez frezy CNC lub inne narzędzia do obróbki, a choćby nadają się do użytku w przestrzeni kosmicznej zgodnie z wynikami testów NASA ASTM E1559. Materiał Windform XT 2.0, który został użyty do produkcji klamer, to materiał na bazie poliamidu wypełniony węglem, aby zapewnić najlepsze adekwatności mechaniczne drukowanego obiektu.

Windform XT 2.0 charakteryzuje się wysoką sztywnością, doskonałą wytrzymałością i zmniejszoną wagą. Co najważniejsze, może zagwarantować wysoką dokładność wymiarową, co pozwala na tworzenie tak bardzo dopasowanych obiektów na zamówienie. Połączenie stylu Scunzaniego, z możliwościami projektowymi MHOX, doświadczeniem CRP w zakresie druku 3D oraz zaawansowanymi adekwatnościami materiału Windform stanowi szkielet dla pełnego, cyfrowego cyklu twórczego możliwego dzięki drukowi 3D i daje nam pierwsze spojrzenie na procesy produkcji odzieży przyszłości.
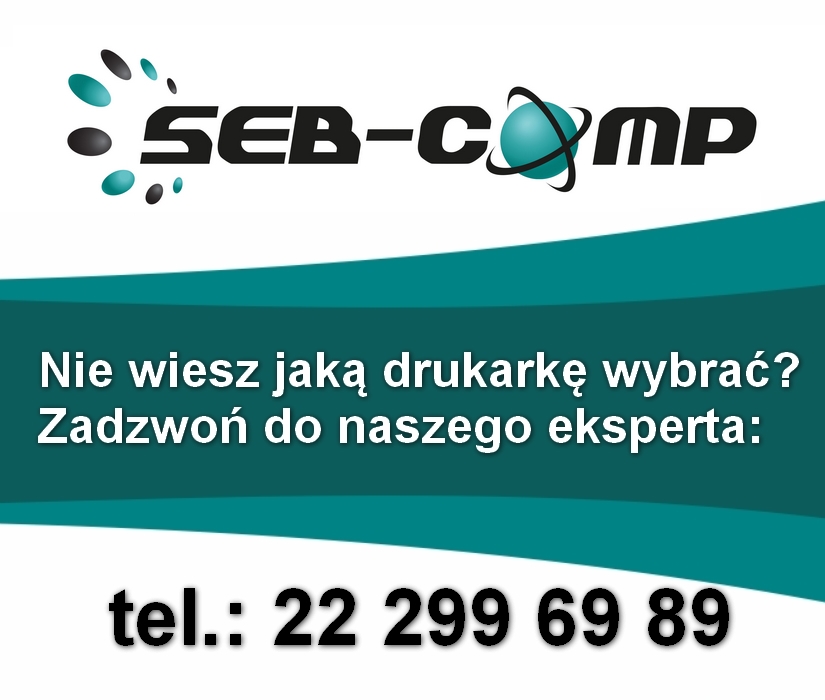
Żródło: https://all3dp.com