Zanurzanie części
Skonfiguruj obwód elektryczny, podłączając elektrody do zasilacza. Anoda musi być przymocowana do metalu tworzącego powłokę. Katoda zostanie podłączona do części. Przytnij metalowy drut na odpowiednią długość i ukształtuj go tak, aby wydrukowana w 3D, zagruntowana i wyczyszczona część mogła w nim osiąść. Niektóre wydruki 3D chcą unosić się na wodzie, więc w razie potrzeby przytrzymaj je drutem. Pamiętaj, aby okresowo zmieniać położenie części podczas powlekania, w przeciwnym razie zespawa się ona z drutem. Napełnij szklany lub plastikowy pojemnik odpowiednim elektrolitem i upewnij się, iż część, która ma zostać pokryta powłoką, jest całkowicie zanurzona.
Galwanizacja części
Wszystko jest skonfigurowane i możesz włączyć zasilanie. Potrzebny prąd zależy od grubości, powierzchni i objętości zbiornika Twojego modelu. Istnieją kalkulatory online , które pomogą Ci obliczyć wymagane napięcie. Aby uzyskać najlepsze rezultaty, warto zwiększać moc, ponieważ osadzona warstwa stopniowo staje się grubsza. Zbyt duży prąd spowoduje nierównomierne pokrycie powłoką z szorstkimi i ziarnistymi osadami oraz szybszą degradację elektrolitu. Słaby prąd spowoduje niewystarczające osadzanie metalu, co doprowadzi do cienkiej lub nierównomiernej powłoki.
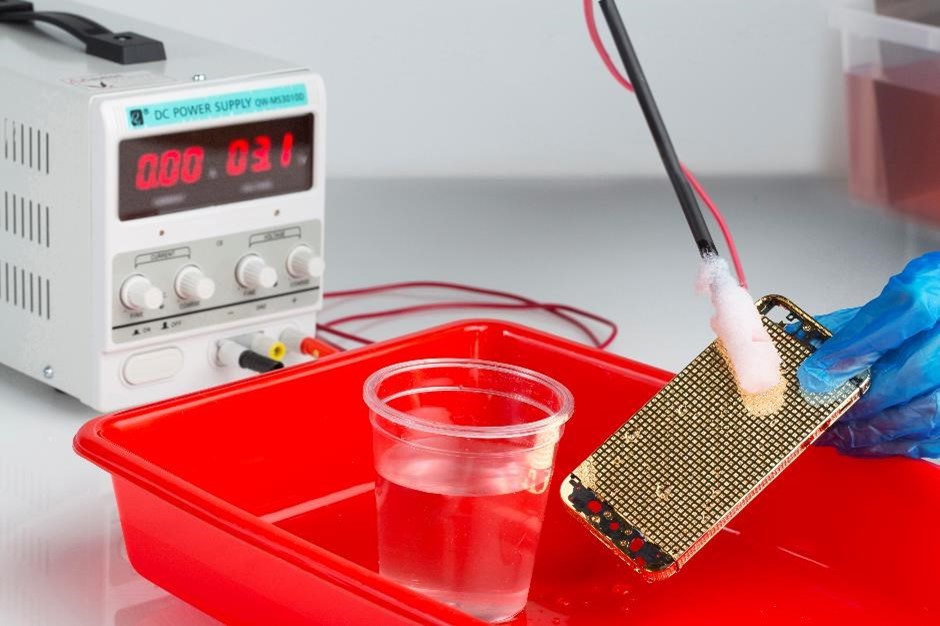
Dalsza obróbka części
Część galwanizowaną można następnie dalej pokrywać innymi metalami, takimi jak nikiel, złoto lub pallad. Można to zrobić poprzez dalszą elektrolizę lub innymi metodami, takimi jak powlekanie szczotkowe. Część można również czyścić chemicznie, aby jeszcze bardziej zwiększyć współczynnik odbicia folii.Galwanizacja wydruków 3D
Rozwiązywanie problemów z galwanizacją

Galwanizacja to złożony proces wymagający wysokiego poziomu staranności i doświadczenia, aby uzyskać zadowalające rezultaty. W tej sekcji podsumowano niektóre z najczęstszych wad, sposób ich powstawania i co można zrobić, aby ich uniknąć.
Wady i problemy z geometrią części
Geometria części odgrywa kluczową rolę w zagwarantowaniu sukcesu galwanizacji. Konwencjonalnie produkowane podłoża wykonane metodą formowania wtryskowego tworzyw sztucznych lub odlewania metali często wykazują nieregularności powierzchni, które utrudniają choćby osadzanie metalu. Na przykład zimne zamknięcia występują, gdy materiały twardnieją na różnych etapach procesu wtrysku, pozostawiając widoczne ślady lub linie przepływu. Wżery, inny powszechny problem, odnoszą się do małych otworów na powierzchni podłoża.
Ich odpowiednikami w dziedzinie druku 3D są linie warstw i problemy z niedostatecznym lub nadmiernym wytłaczaniem materiału. Te zjawiska specyficzne dla procesu powodują odchylenia od ostatecznych wymiarów części. Należy je obsługiwać poprzez szlifowanie i gruntowanie przed galwanizacją, ponieważ tak znaczących nieregularności nie można naprawić po osadzeniu folii metalowej.
Nawet celowe geometrie części, takie jak ostre krawędzie lub skomplikowane wzory, takie jak kratki, mogą powodować problemy podczas powlekania z powodu problemów z rozprowadzaniem prądu. Gęstość prądu jest wyższa przy ostrych krawędziach, co oznacza, iż w tych obszarach wystąpi nadmierna powłoka, co doprowadzi do kruchej warstwy, która łatwo pęka. Przeciwieństwem tego jest zacienianie, które można rozumieć podobnie do rzucania cienia przez słońce. Części podłoża, które są przykryte anodami, będą otrzymywać mniej osadów. Można to rozwiązać, przestawiając anody lub ciągle obracając podłoże w elektrolicie w celu rozprowadzenia ekspozycji części.
Słaba przyczepność
Słaba przyczepność między podłożem a wykończeniem metalu może mieć kilka przyczyn. Po pierwsze, jeżeli część plastikowa i powłoka przewodząca nie połączą się dobrze, rozdzielą się, a wraz z nimi powłoka metalowa, choćby jeżeli została osadzona tak, jak powinna. Znalezienie odpowiedniej kombinacji powłoki plastikowej i lakierniczej jest kluczowe. Oprócz dobrych adekwatności wiążących, powierzchnia robocza musi być również wolna od smaru, kurzu lub utleniania, które osłabiają przyczepność. Ponieważ plastik i metal rozszerzają się inaczej pod wpływem ciepła, choćby idealna powłoka może pękać i odklejać się z czasem, jeżeli część zostanie wystawiona na takie środowisko. W takim przypadku najlepszym rozwiązaniem może być galwanizacja z użyciem innej kombinacji materiałów lub pójście drogą druku 3D metalu.
Nierównomierne powlekanie
Załóżmy, iż wykończona powłoka jest nie tylko matowa, ale również szorstka. W takim przypadku elektrolit może ulec degradacji i zanieczyszczeniu cząsteczkami, które osadzą się na podłożu, pozostawiając nierówną powłokę. Filtrowanie lub wymiana elektrolitu pomoże.
Nadmierny prąd prowadzi również do nierównomiernego powlekania; w związku z tym zmniejszenie prądu często łagodzi problem. Pęcherzyki tworzące się na podłożu są zwykle znakiem ostrzegawczym. Jednak jeżeli prąd jest zbyt niski, powłoka może być zbyt cienka lub choćby nierówna i niekompletna. Znalezienie adekwatnej równowagi jest jednym z najważniejszych aspektów sukcesu galwanizacji.
Matowe i zamglone platerowanie
Może to być frustrujące, gdy powłoka jest udana, ale nie wykazuje pożądanego połysku i odbicia. Istnieje wiele powodów, dla których tak się stało. Przyczyną może być nierównowaga chemiczna, taka jak zbyt duża ilość siarczanu, kwasu chromowego lub zanieczyszczeń rozpuszczonych w elektrolicie, więc zmiana elektrolitu może poprawić wyniki. Innym powodem mogą być nieprawidłowe temperatury. Temperatury pomiędzy 130 a 140°F są idealne zarówno dla kąpieli, jak i podłoża.
Nieprawidłowa gęstość prądu lub zepsuty zasilacz powodujący przerwanie prądu mogą być również przyczyną. Sama część może być również umieszczona zbyt wysoko w pojemniku. Upewnij się, iż znajduje się co najmniej cztery cale pod powierzchnią. Na koniec, niewystarczające płukanie między etapami galwanizacji może prowadzić do pozostałości chemicznych lub brudu i późniejszego zmatowienia. jeżeli żadna z tych metod nie przyniesie oczekiwanych rezultatów, użycie rozjaśniacza może również pomóc w poprawie końcowego rezultatu, ponieważ zapobiega tworzeniu się dużych kryształów na części, dzięki czemu staje się ona bardziej błyszcząca.Galwanizacja wydruków 3D
Galwanizacja – zalety i wady

Podobnie jak każda technologia, galwanizacja ma swoje zalety i wady, z których część została już wymieniona w artykule i zostanie tutaj podsumowana. Oprócz typowych kwestii związanych z galwanizacją, należy wziąć pod uwagę kilka innych, łącząc ją z drukiem 3D. Poniższa lista podsumowuje te zalety i wady.
Zalety galwanizacji
- Ulepszony wygląd powierzchni
- Chroni materiał podłoża przed zużyciem mechanicznym, korozją i matowieniem
- Poprawia adekwatności części, takie jak wytrzymałość na rozciąganie, sztywność i waga
- Tworzy nowe adekwatności, takie jak magnetyzm lub przewodnictwo elektryczne
- Umożliwia powlekanie różnych metali, w tym miedzi, cyny, niklu, złota, palladu, chromu i innych
- Niskobudżetowa alternatywa dla druku 3D w metalu, która wzbogaca elementy plastikowe o cechy metalu
Wady galwanizacji
- Choć jest to tańsze niż drukowanie 3D z metalu, wymagane materiały są drogie i zwiększają koszt finalnej części
- Żmudny i ręczny proces z defektami specyficznymi dla procesu, takimi jak zimne zamknięcia, wżery, ostre krawędzie, punkty rozszczepienia i utrata przyczepności, które sprawiają, iż proces ten jest trudny do opanowania, szczególnie w przypadku konfiguracji hobbystycznej
- Różne adekwatności rozszerzalności cieplnej plastiku i metalu mogą z czasem prowadzić do pęknięć i oddzielenia się powłoki od podłoża
- Właściwości mechaniczne nie są zbliżone do adekwatności części metalowych
- Długi proces, który trwa od kilku godzin do kilku dni, w zależności od wymaganego wykończenia
- Materiały toksyczne, które tworzą niebezpieczne odpady i mogą szkodzić środowisku, jeżeli są nieprawidłowo obsługiwane i utylizowane
Galwanizacja wydruków 3D
Kto stosuje galwanizację?

Ponieważ galwanizacja jest dobrze znaną techniką wykańczania, większość sektorów produkcyjnych, w tym produkcja addytywna, wykorzystuje ją w wybranych zastosowaniach w celu poprawy cech części, takich jak przewodność, trwałość, poprawa wyglądu lub wytrzymałość. Takie branże obejmują przemysł motoryzacyjny, lotniczy, elektroniczny, medyczny i modowy. W tym ostatnim jest ona wykorzystywana przez projektantów obuwia i producentów biżuterii, aby nadać swoim produktom bardziej luksusowy wygląd i charakter. Galwanizacja plastikowego lub metalowego pierścionka mikroskopijną warstwą złota będzie znacznie tańsza, ale zapewni ten sam elegancki wygląd. Pozwala również producentom bez dostępu do sprzętu złotniczego na modernizację swoich drukowanych w technologii 3D plastikowych części przy stosunkowo niskich kosztach.
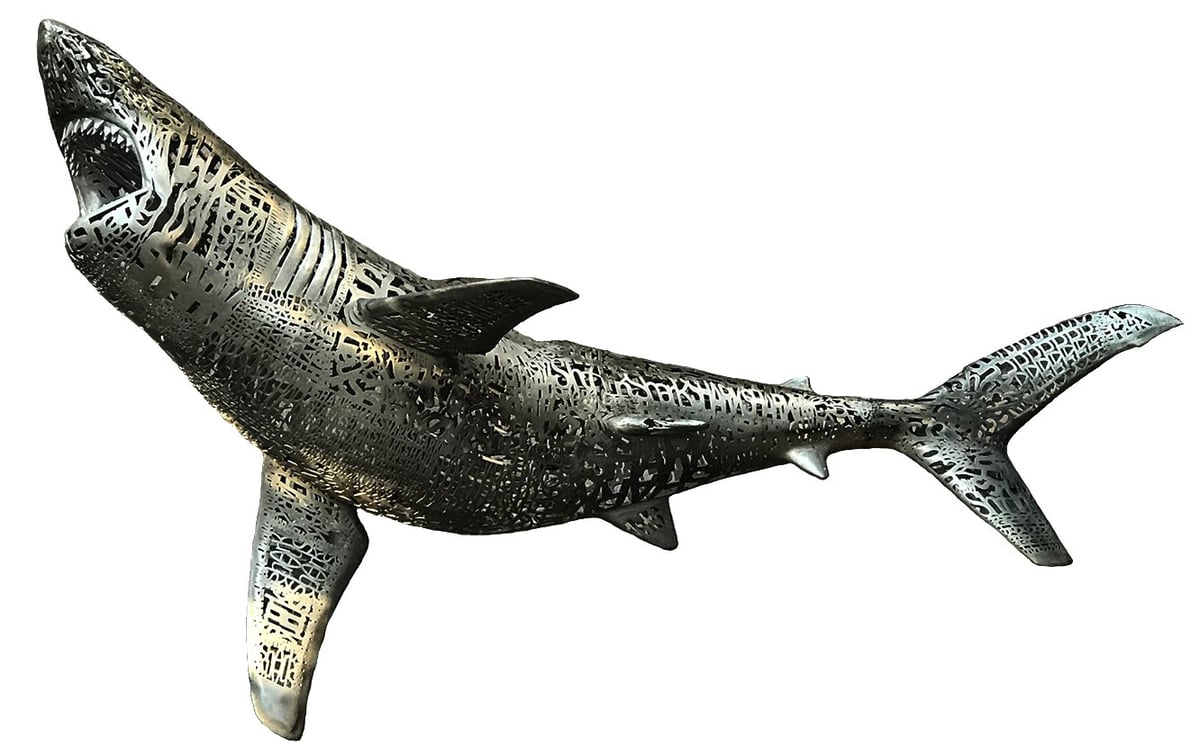
Dotyczy to również hobbystów, takich jak modelarze i twórcy miniatur, którzy chcą zamienić swoje wydrukowane w technologii SLA 3D projekty w błyszczące, cięższe figurki lub realistyczne rekwizyty przypominające polerowany metal. Wielu artystów łączy również wszechstronność druku 3D z oszałamiającym wyglądem galwanizacji, aby tworzyć dzieła sztuki, takie jak „Emptiness of Shark” Michaela Cardacino, pusta 6-stopowa rzeźba rekina, która została wydrukowana metodą SLS na aparacie EOS P730 w kilku częściach, zmontowana i pokryta galwanicznie miedzią i niklem przez Repliform.
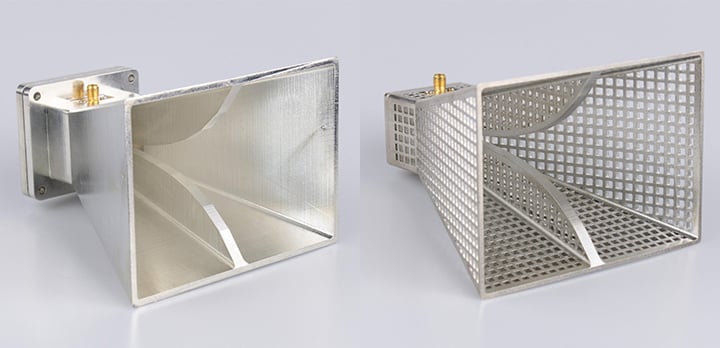
Przechodząc do przemysłowego druku 3D i galwanizacji, Elliptika, specjalista w zakresie produktów i rozwiązań radiowych i mikrofalowych, wykorzystuje produkcję addytywną do projektowania złożonych anten radiowych, które są o 80% lżejsze przy tej samej wydajności co ich w pełni metalowe odpowiedniki. Firmie udało się również drukować w technologii 3D wysokowydajne części anten przy koszcie niższym o 90% w porównaniu z konwencjonalnymi metodami, dzięki czemu produkcja części o małej objętości jest szybsza i znacznie bardziej opłacalna. W przemyśle motoryzacyjnym galwanizacja jest również często stosowana w celu poprawy atrakcyjności wizualnej samochodów koncepcyjnych lub produkcji reprodukcji części zamiennych do klasycznych modeli samochodów.
Gdzie można wykonać powłokę galwaniczną części?

Kilka usług drukowania 3D na żądanie oferuje galwanizację, zwaną również po prostu platerowaniem, jako rodzaj wykończenia wydruku 3D. Wygodnie jest po prostu przesłać plik cyfrowy, a te firmy zajmą się drukowaniem, przygotowaniem i platerowaniem Twojej części.
źródło: all3dp
