Zatonąć czy popłynąć?

Pierwsze pytanie, które większość ludzi może zadać, gdy przedstawi im się możliwość druku 3D kajaka, brzmi: “Czy to faktycznie zadziała?”.
Chociaż z pewnością nie dzieje się to na dużą skalę, kilka osób na świecie podjęło się tego interesującego wyzwania inżynieryjnego. W szczególności Jim Smith z Grassroots Engineering zasłynął z wydrukowania w 3D pierwszego w pełni funkcjonalnego kajaka.
Drukowanie kajaka nie jest łatwym zadaniem, a osoby zainteresowane tym wyzwaniem musiałyby rozwiązać różne problemy, w tym wodoodporność, drukowanie dużych części bez odkształceń i pęknięć oraz upewnienie się, iż gotowa łódź jest zarówno lekka, jak i wytrzymała.
W tym artykule poznamy kulisy fantastycznego projektu Jima Smitha, a następnie przyjrzymy się, jak firma o nazwie Melker ze Szwecji która wykorzystuje druk 3D oraz drewno i filamenty z materiałów recyklingowych.
Jim Smith: Pierwszy na świecie

Jim Smith to człowiek, który postanowił przekroczyć granice swojej pomysłowości i stał się znany jako pierwszy człowiek, który zbudował swój własny, funkcjonalny kajak wydrukowany w 3D.
Niemniej jednak, wymagało to nie lada umiejętności i niecodziennych zasobów, co oznacza, iż nie jest to projekt, który można po prostu wydrukować w weekend.
W całości kajak ma 16,7 stopy (~5 m) długości na 1,7 stopy (~ 0,5 m) szerokości i waży 64,58 lb (29,29 kg). Składa się z 28 różnych części wydrukowanych z filamentu ABS, a jedyne części użyte do jego złożenia to śruby maszynowe, mosiężne wkładki gwintowane i trochę silikonowej masy uszczelniającej.
Projekt początkowo opierał się na kajaku Siskiwit Bay autorstwa Bryana Hansela, ale został mocno zmodyfikowany pod kątem druku 3D.
Jim zdecydował się również na podejście “technicolor”, drukując wszystkie sekcje z różnokolorowego ABS-u, a rezultat wygląda całkiem dobrze!
Wyposażenie

Najważniejszym elementem tego projektu była drukarka 3D.
Na szczęście Smith pracuje jako inżynier w 3D Systems, więc był w stanie zmodyfikować swoją własną, zbudowaną na zamówienie, wielkogabarytową drukarkę 3D w celu ukończenia projektu: dodając zamkniętą komorę roboczą.
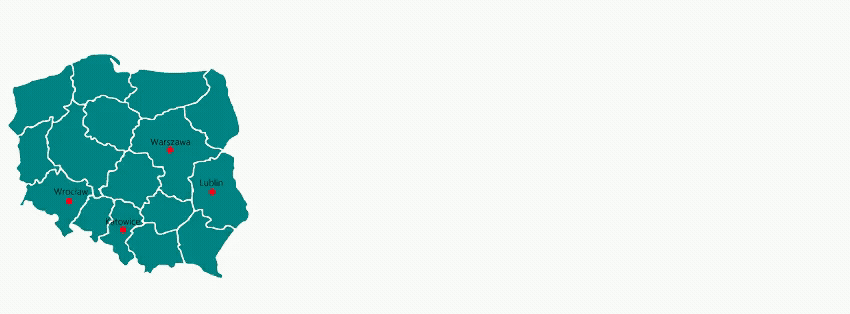
Jak być może wiesz, jednym z głównych problemów związanych z drukowaniem dużych części w ABS jest to, iż niespójna temperatura otoczenia i przeciągi powietrza w warsztacie mogą prowadzić do pęknięć lub wypaczeń. Ponadto, im większa część, tym większe mogą być pęknięcia lub wypaczenia. Aby temu zapobiec, zamknięta komora była pasywnie ogrzewana przez powierzchnię konstrukcyjną podczas drukowania, osiągając stabilną temperaturę od 65 do 70 °C (149-158 °F).
Aby umożliwić drukowanie, oryginalny projekt musiał zostać pocięty na kawałki, które były drukowane pojedynczo. Wydruki odbywały się przy wysokości warstwy 0,65 mm, aby skrócić czas drukowania, ale i tak zakończenie drukowania wszystkich części zajęło około 42 dni!
Szczelnie zamknięty

Jakkolwiek trudne wydawało się to zadanie, złożenie wszystkich części razem okazało się dość prostą sprawą, polegającą na zmontowaniu ich dzięki śrub maszynowych. Każda sekcja została wyposażona w mosiężne wkładki gwintowane, pozwalające na zamocowanie kolejnej sekcji. Wydaje się, iż to był cały sprzęt potrzebny do utrzymania części razem!
Co zaskakujące, Jim musiał jedynie użyć silikonowej masy uszczelniającej pomiędzy sekcjami, aby stworzyć uszczelnienie. Podczas gdy domowe drukarki 3D nie są znane z tworzenia całkowicie wodoszczelnych struktur, zbudowana przez Jima maszyna wyraźnie sprostała temu zadaniu.
Kiedy wszystko zostało złożone i uszczelnione, pozostało tylko sprawdzić, czy unosi się na wodzie. I, wierzcie lub nie, udało się! To niesamowite, co można osiągnąć dzięki odrobinie (lub dużej) pomysłowości i wytrwałości.
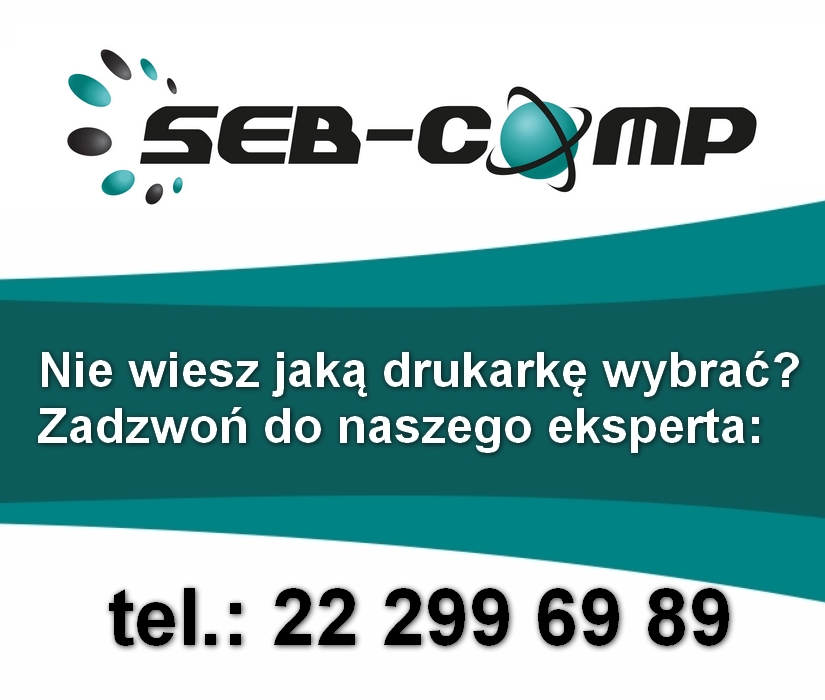
Żródło: https://all3dp.com