Mirko Filler lubi drogie rzeczy, najlepiej z karbonu. Nic dziwnego, to jego zabawki. Beast Components to mały fragment jego biznesu, ale z nieukrywaną dumą oprowadzał nas po manufakturze, gdzie powstają.
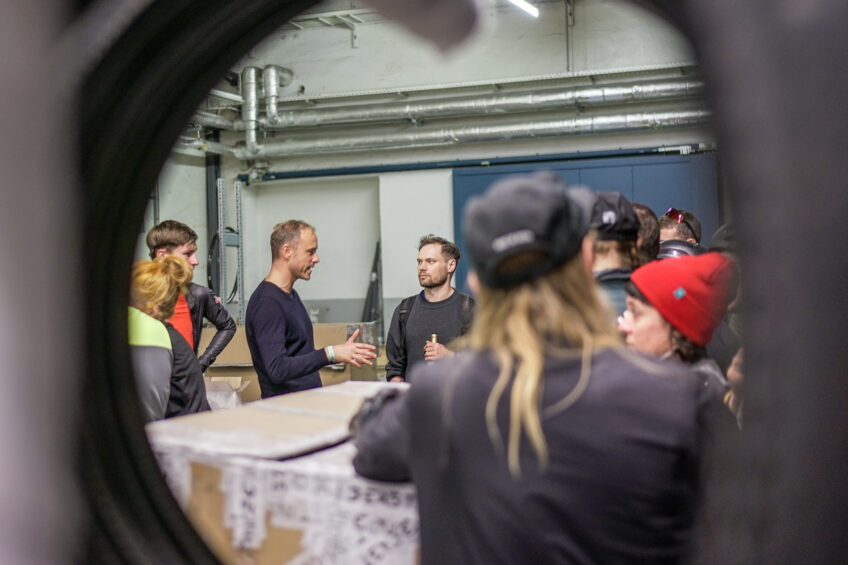
Uwaga na marginesie – można odnieść wrażenie, iż Drezno i okolica stały się dla Niemiec tym czym dla polski Wrocław, to miasto i region w zadziwiający sposób przyciągają ludzi związanych z rowerami. Podobnie wiele się dzieje i powstają kolejne firmy, towarzyszy temu ożywczy ferment, realizowane są imprezy takie jak Bespoked Handmade Show, żyje tzw. środowisko. Wizyta w Beast Components była jedną z kilku, która odbyłem w ciągu ostatnich miesięcy, a jeżeli interesują was podobne historie zza kulisów zarzyjcie koniecznie do reportaży z Actofive, Qvist i Bike24.
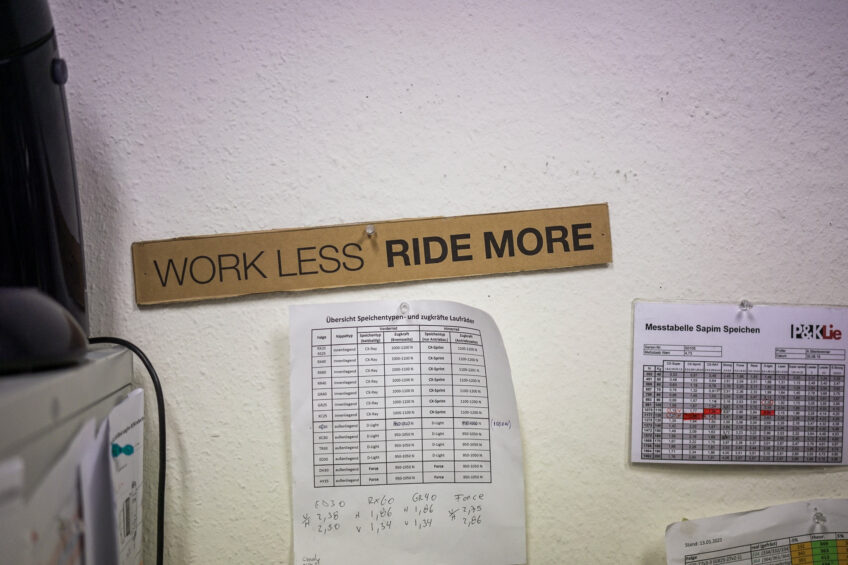
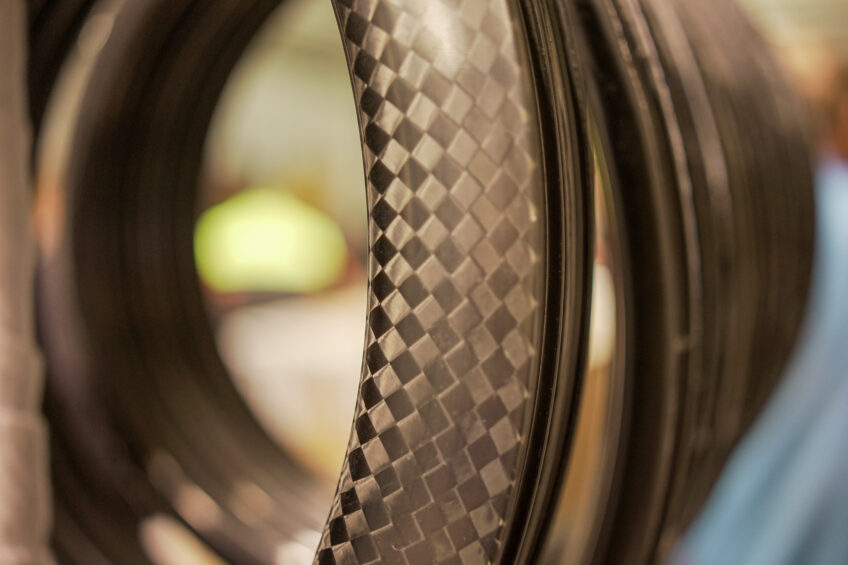
„Zwiedzanie” siedziby Beast Components nie jest możliwe na co dzień, firma jest zgrabnie ukryta w kompleksie budynków w przemysłowej dzielnicy Drezna, gdzie produkowano amunicję w czasie I Wojny Światowej. Trafienie na miejsce jest o tyle utrudnione, iż komponenty rowerowe to nie jest podstawowa działalność zakładu Carbo Life, gro dochodu przynosi owszem karbon, ale to komponenty do pojazdów z osób z niepełnosprawnościami. Beast Components to tym samym jakby produkt uboczny, ale z wykorzystaniem doświadczeń i umiejętności zdobytych do tworzenia tych pierwszych. Wszystko bowiem powstało przez przypadek, a raczej na skutek nieszczęśliwego wypadku na motocyklu jednego z kolegów Mirko, w wyniku którego ten został sparaliżowany.
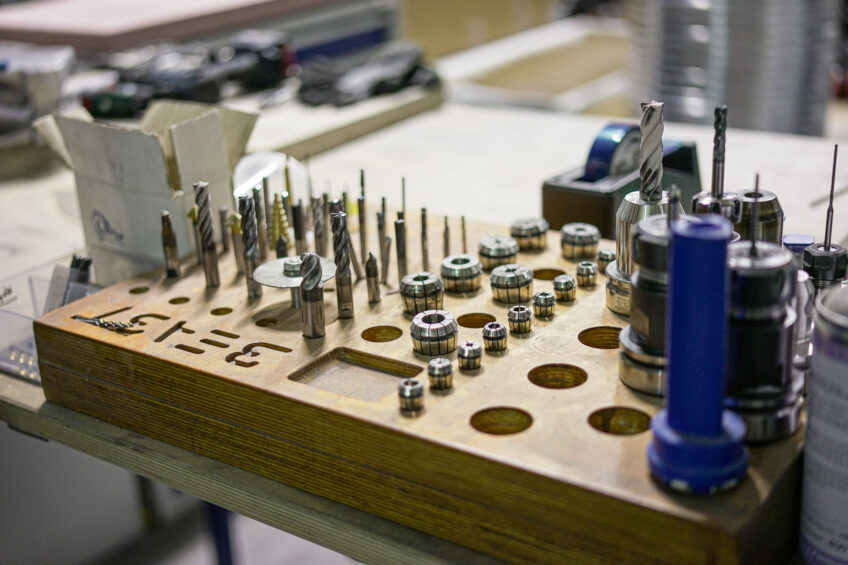
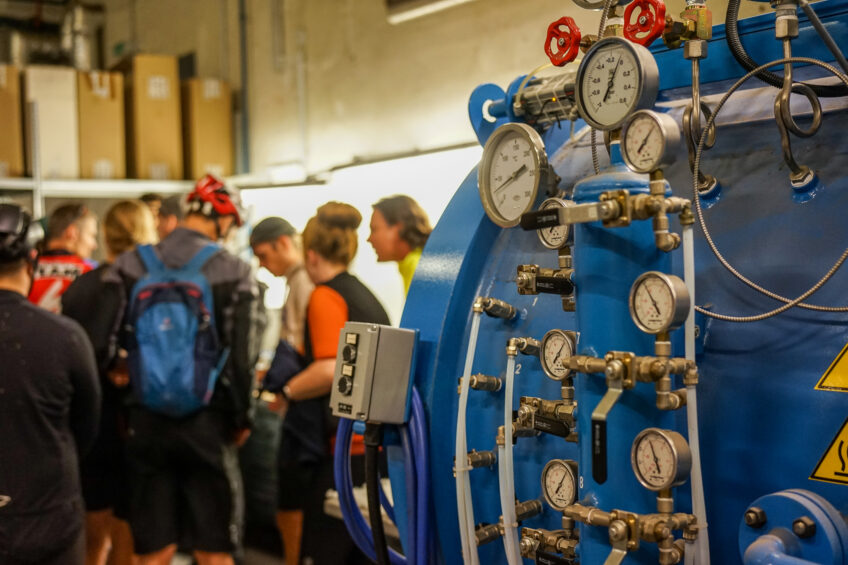
Generalnie rzecz ujmując komponenty w zakładzie powstają w sposób bardzo podobny, jak niemal u każdego innego producentów części z kompozytów. Co oznacza bardzo dużą ilość manualnej, żmudnej pracy. To, co odróżnia Beast Components od konkurencji, to fakt, iż poza doświadczeniem, bardzo duży udział w powstawaniu produktów finalnych ma projektowanie i testowanie. I to już na etapie tworzenia komponentów w komputerze, gdzie zaawansowane oprogramowanie pozwala unikać powstawaniu słabych miejsc konstrukcji. To znów nie byłoby możliwe – i tu musze cofnąć się głębiej w przeszłość – bez studiów na politechnice w Dreźnie (TU Dresden), gdzie spotkali się Mirko, Thomas Bartl, czyli w tej chwili główny inżynier odpowiedzialny za rozwój. Trzecia osoba tworząca firmę to ich były wykładowca Andreas Freund, zajmujący się w tej chwili zarządzaniem i sprzedażą. Wyjątkowość zaś Beast Components ma polegać na symulowaniu komponentów, zanim powstaną. A potem ich sprawdzaniu, gdy już istnieją, na własnych stanowiskach testowych, by na wszelki upadek upewnić się, iż teoria pokrywa się z praktyką.
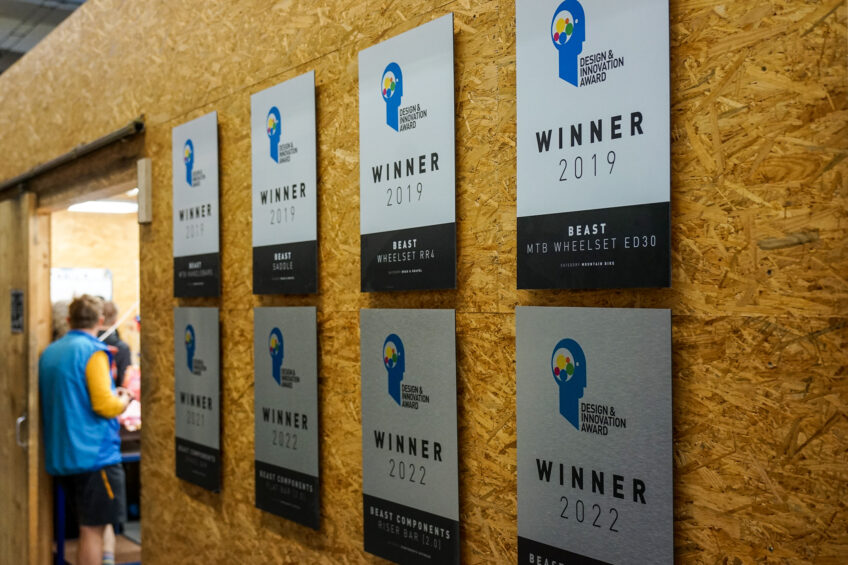
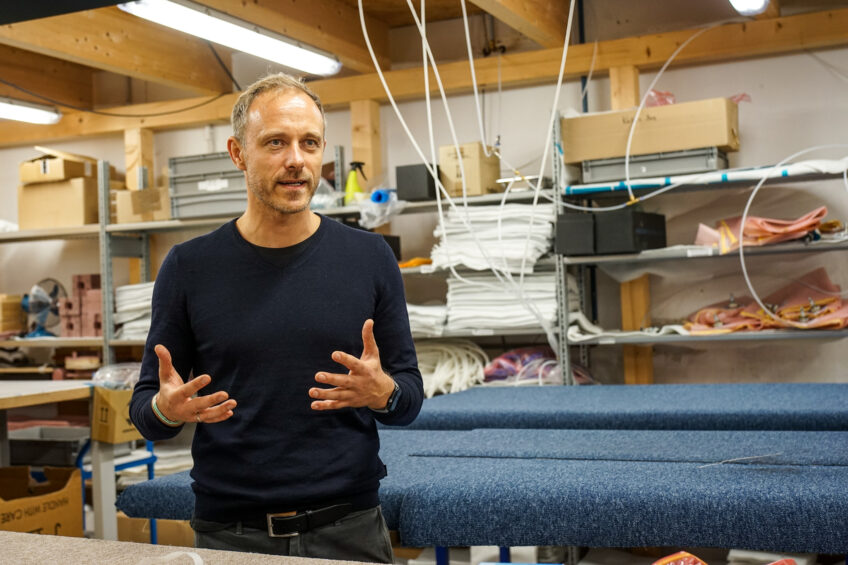
Carbo Life i Beast Components to nie koniec firmowej wyliczanki, do której dochodzi trzecia firma, czyli Realize Engineering. Wykorzystanie unikalnych, wspomnianych kompetencji przekłada się w niej na różne projekty dla przemysłu lotniczego i kosmicznego. Symulowanie części z kompozytów to wyższa szkoła jazdy niż w przypadku metali, dochodzą zagadnienia w stylu sprężystość ortotropowa, czy zależności temperaturowe albo współczynnik odkształcenia. Nic wam to nie mówi? To także dla mnie niemal czarna magia – ale znajduje odbicie w jak najbardziej realnych, działających częściach rowerowych. A te miałem na miejscu w rękach. Potwierdzeniem jakości są otrzymywane seryjnie prestiżowe nagrody Eurobike Design & Innovation Award.
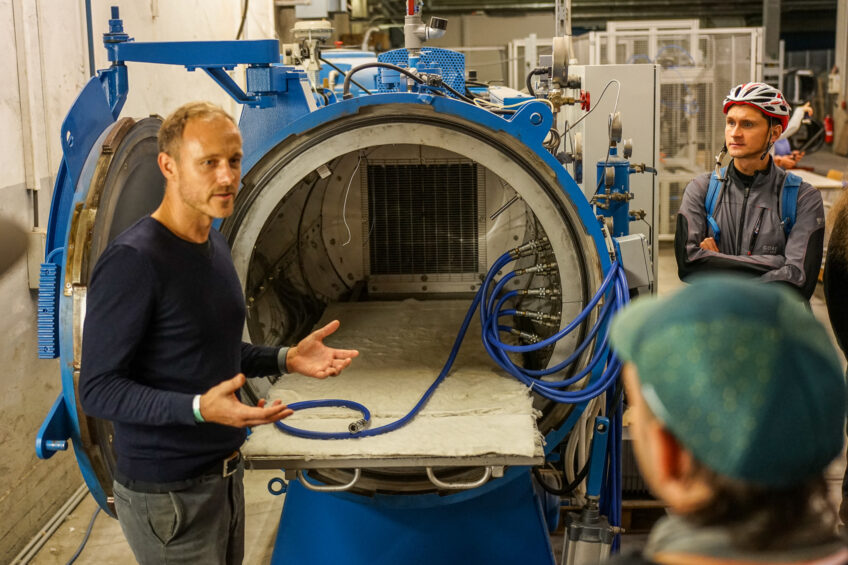
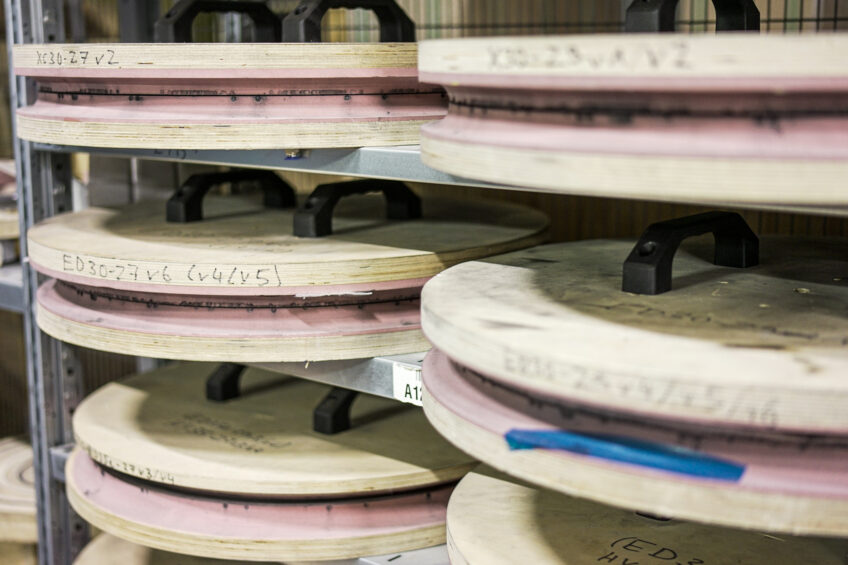
Drobne zastrzeżenie, o ile zajrzeć w firmie mogłem niemal wszędzie, to pokazano nam tylko elementy układanki, skrzętnie chowając zastrzeżone elementy procesów. A może dostrzeżenie na zdjęciach coś, co mi nie mówi nic, a wam zdradzi wielką tajemnicę? Jakby coś, proszę o wiadomość na privie! Z chęcią uzupełnię tekst o smaczki.
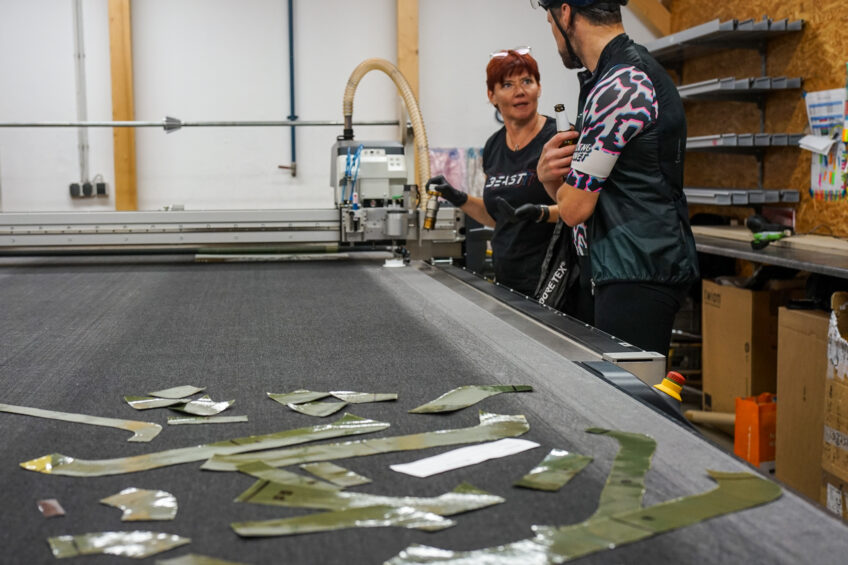
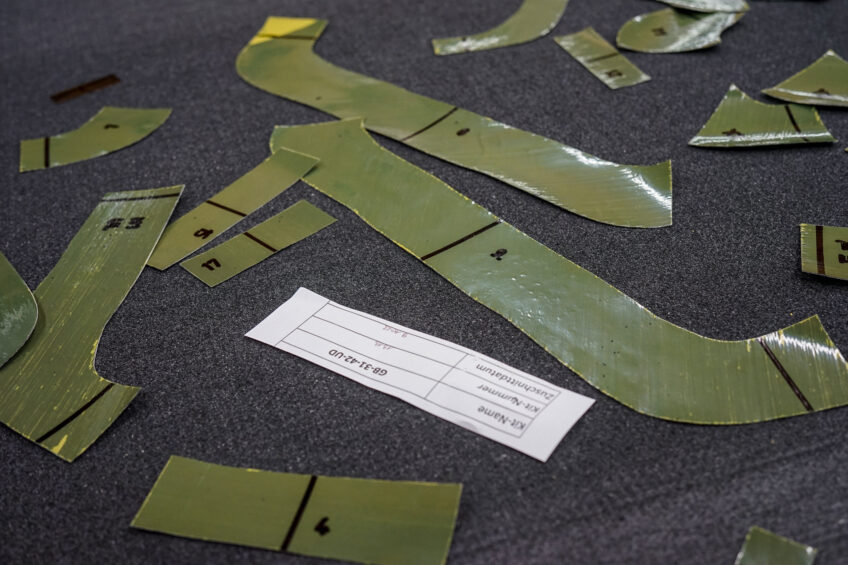
Produkty Beast Components od początku do końca powstają na miejscu, zaczynając życie w lodówce, jako prepregi, czyli włókna węglowe nasączone żywicą.
Po wyciągnięciu, w zależności od rodzaju, muszą być odpowiednio gwałtownie użyte, bo już temperatura pokojowa zmienia ich adekwatności – mówiąc wprost twardnieją. Tu następuje mój ulubiony fragment, czyli bawienie się w wycinanki dzięki wielkiego plotera, dbającego o to, by jak najmniej materiału się zmarnowało.
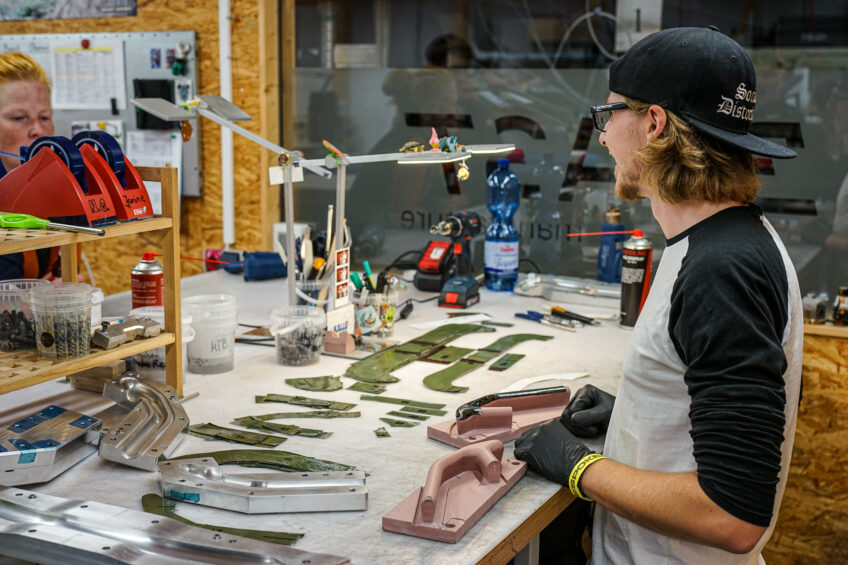
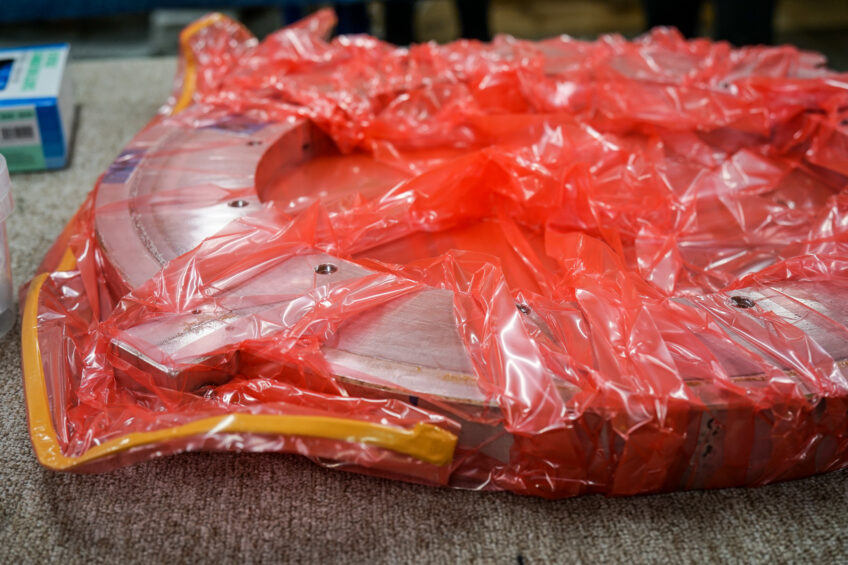
Te fragmenty, jak w klasycznym wykroju na spodnie czy sukienkę, trafiają następnie do „szycia”, a raczej do układania w formie. Do tego, by się nie pogubić, służy oczywiście cały system instrukcji, z opisem fragmentów i wskazówkami, jak je układać. To przepis na produkt, także tajemnica firmy. I metoda kontroli jakości, której ścisłe przestrzeganie ma wyeliminować ludzkie błędy.
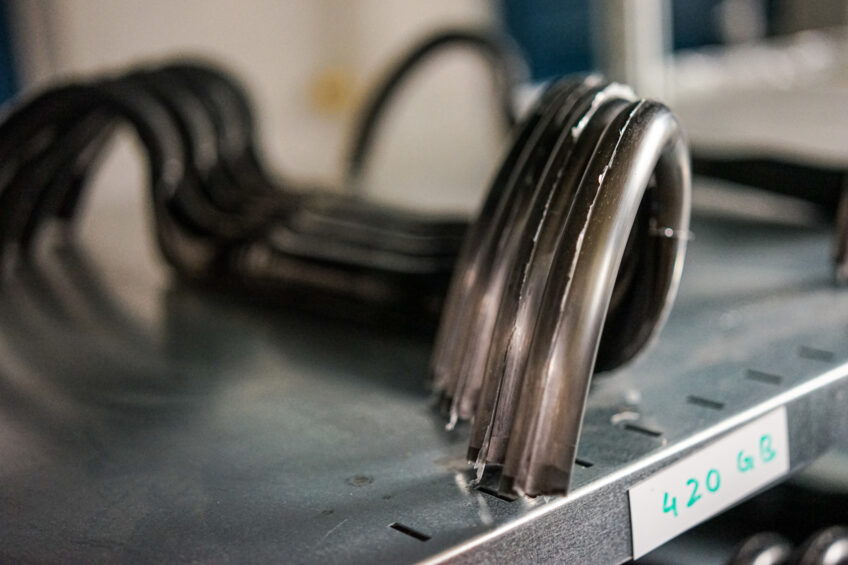
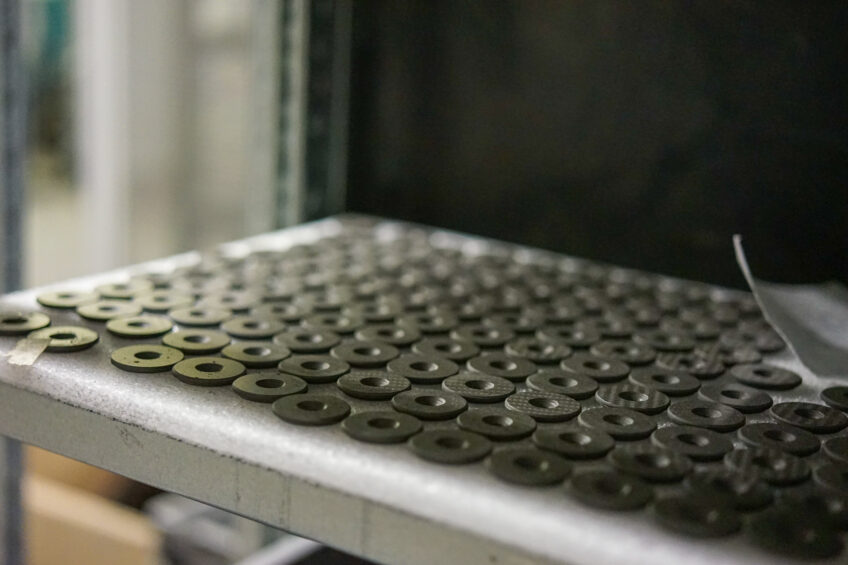
Kierunek włókien, jak na siebie nachodzą, ilość warstw, wszystko ma znaczenie dla finalnych własności komponentu.
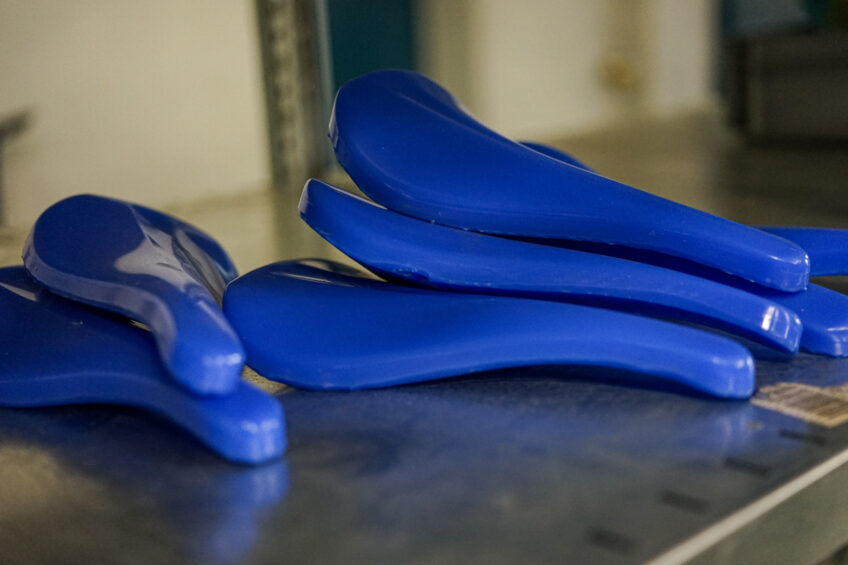
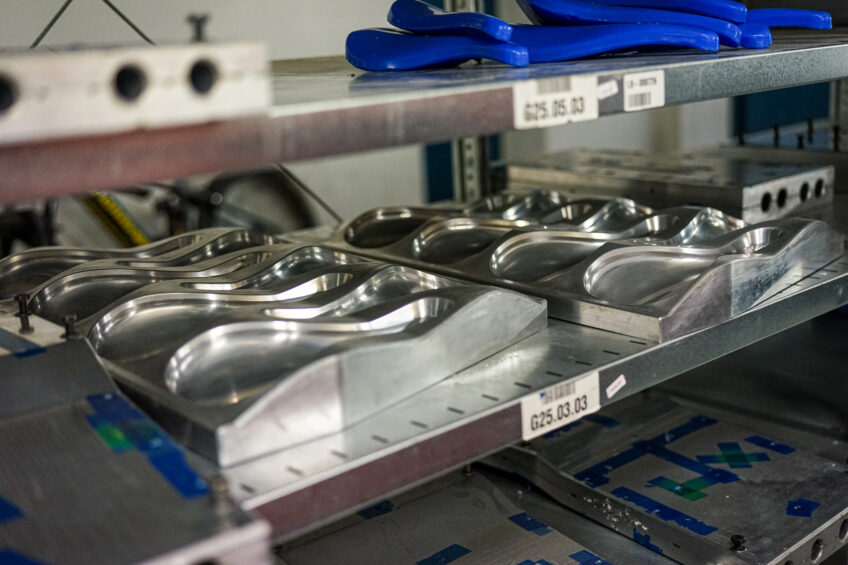
Do uzyskania kształtów służa odpowiednie formy, różnego typu, w zależności od rodzaju komponentów. Mogą być też wykonane z różnych materiałów. Część gotowa do utwardzenia trwafia do próżniowego worka, który powoduje, iż w środku nie będzie bąbelków powietrza, mogącego powodować powstawanie niedoskonałości.
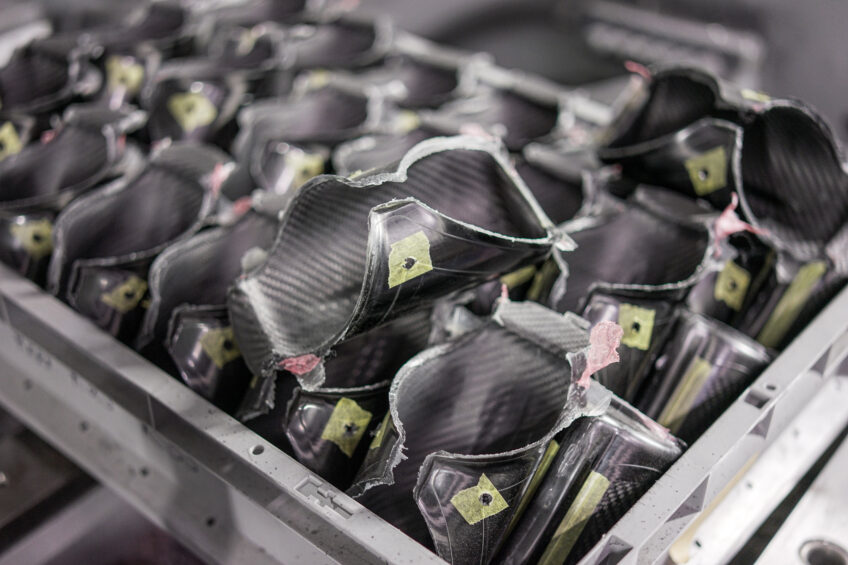
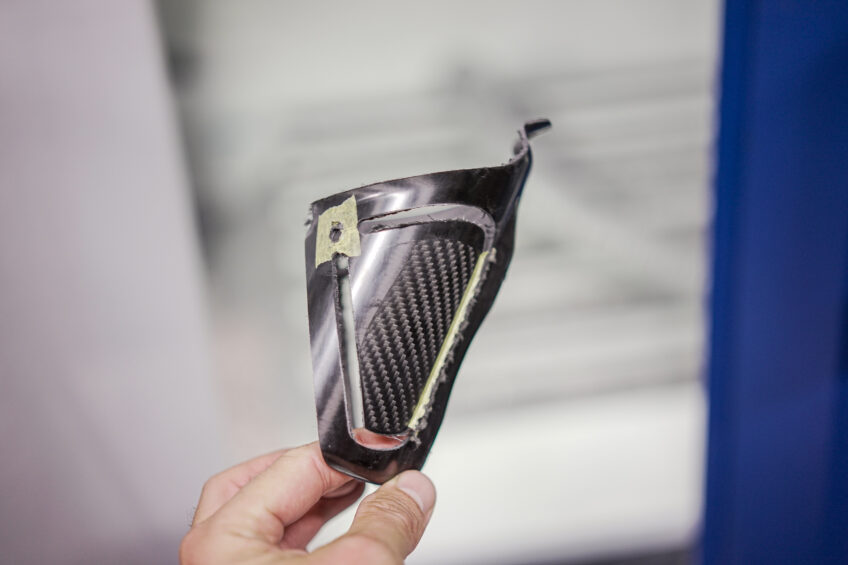
Po utwardzeniu gotowe części wymagają jeszcze wykończenia, jest to nie tylko usuwanie niepotrzebnych fragmentów, ale też wykończenie powierzchni. Jeden z elementów całej układanki to naniesienie specjalnych, firmowych naklejek.
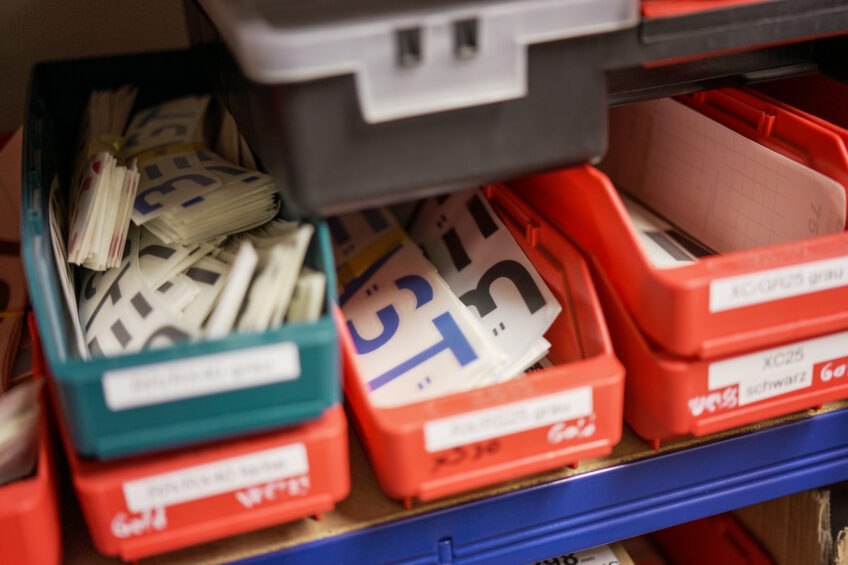
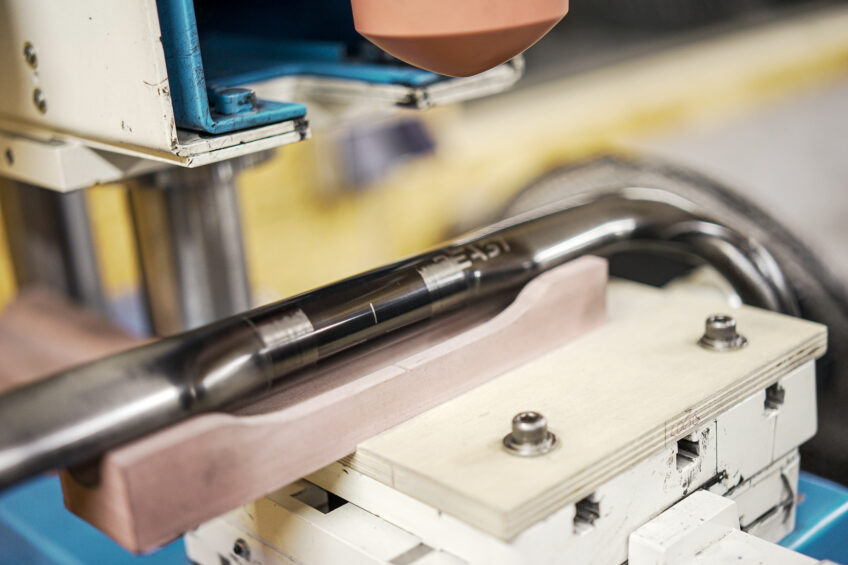
Po wyprodukowaniu komponenty poddawane są testom wytrzymałościowym, na miejscu bada się nie tylko kierownice, ale też np. koła. Wykorzystuje się cały park maszynowy po to, by upewnić się, iż lekkie komponenty będą bezpieczne.
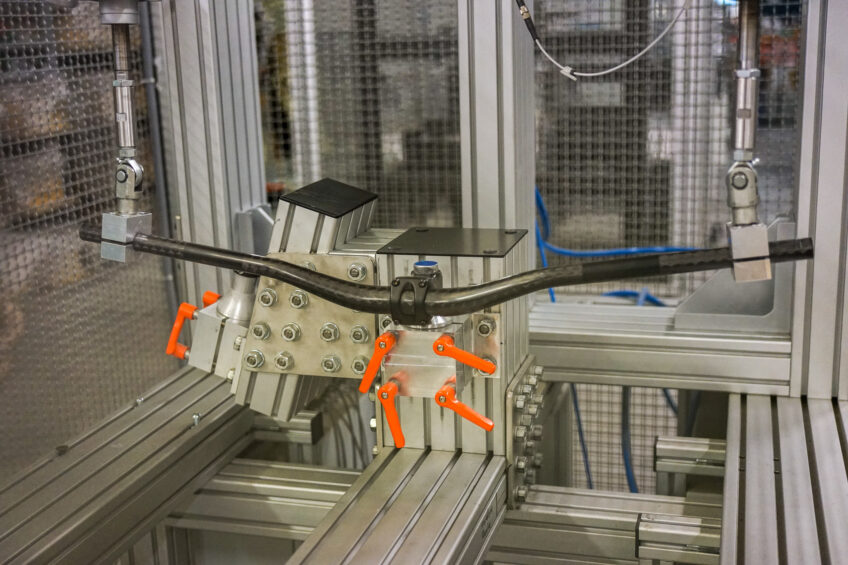
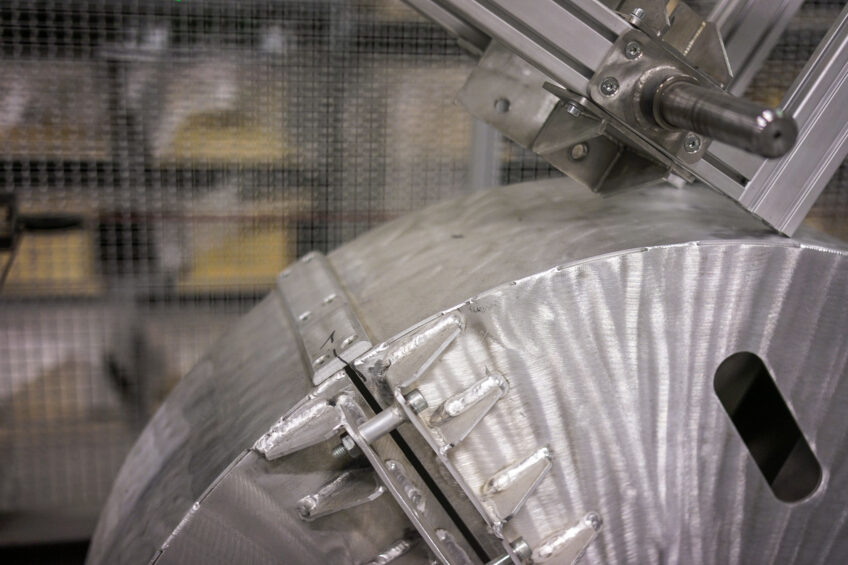
„Element ludzki” wykorzystywany jest także przy budowaniu kół, które firma również ma w ofercie, o opartych na własnych obręczach z karbonu. Tu także wykorzystane są precyzyjne instrumenty pomiarowe i sprawne, doświadczone ręce.
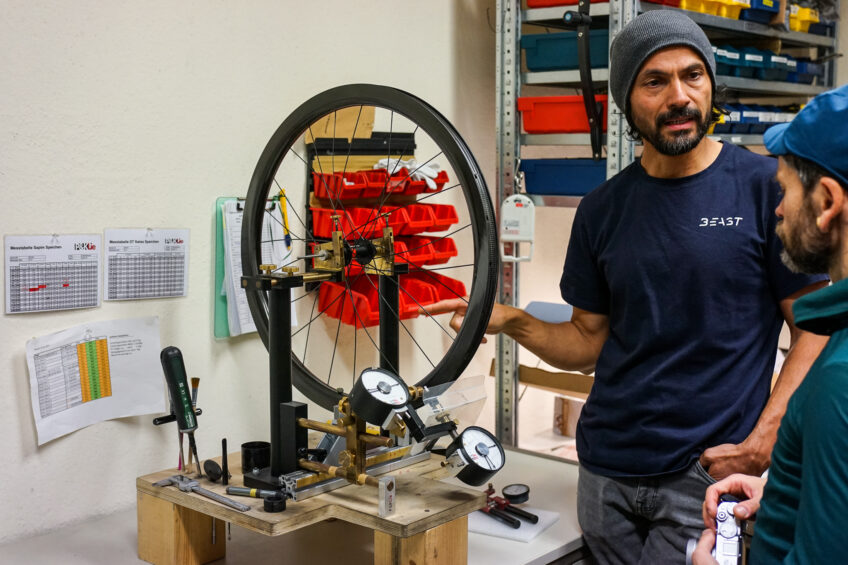
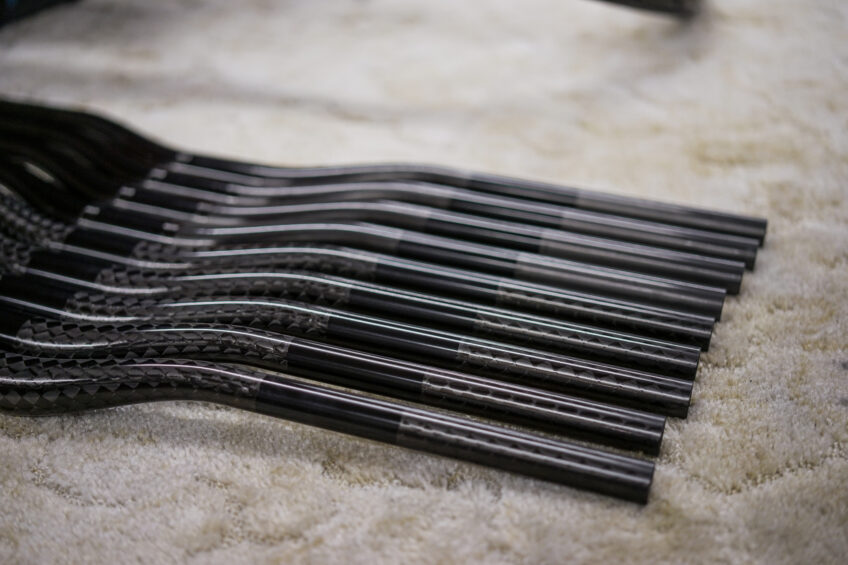
Co mnie zdziwiło najbardziej, to chyba fakt, iż mając możliwość produkcji dla innych branży, gdzie da się zarobić zdecydowanie więcej pieniędzy niż w rowerówce, Beast Components w ogóle istnieje. Co nie znaczy, iż przy całym ich zaawansowaniu są to produkty tanie. Kierownice kosztują ponad 200 euro, siodła 300, koszyk to 100 euro, a koła startują od około 2000 euro. Ma finalne ceny liczone w setkach ma jednak wpływ nie tylko zaawansowanie technologiczne, ale fakt, iż są wytwarzane w Dreźnie, gdzie godzina pracy w firmie to 30 Euro, jak usłyszałem. Macie ochotę by podobne lekkie i mocne cacko wylądowało też w waszym garażu? Pełną ofertę znajdziecie na shop.beast-components.de/